What is Work Order Mangagement? : A Comprehensive Guide
1. Introduction
Work orders are the unsung heroes of industrial efficiency. Whether you're an OEM dispatching service technicians to remote customer sites, or a factory maintenance lead juggling dozens of internal requests, your ability to create, assign, and track work orders defines how well your operations run.
Yet for many industrial teams, work order management still lives in a world of paper forms, emails, spreadsheets—or worse, notepads left in the glovebox of a service van.
In this guide, we unpack how modern work order systems are transforming both field service and internal maintenance. We’ll also show why Makula—built specifically for manufacturers and OEMs—is the only platform purpose-built to handle both.
2. What Is Work Order Management?
Work order management refers to the process of tracking service, repair, or maintenance tasks—from initiation through to closure. It ensures every job is:
- Properly scoped and assigned
- Executed with the right parts and personnel
- Documented for future reference and compliance
A typical lifecycle looks like this:
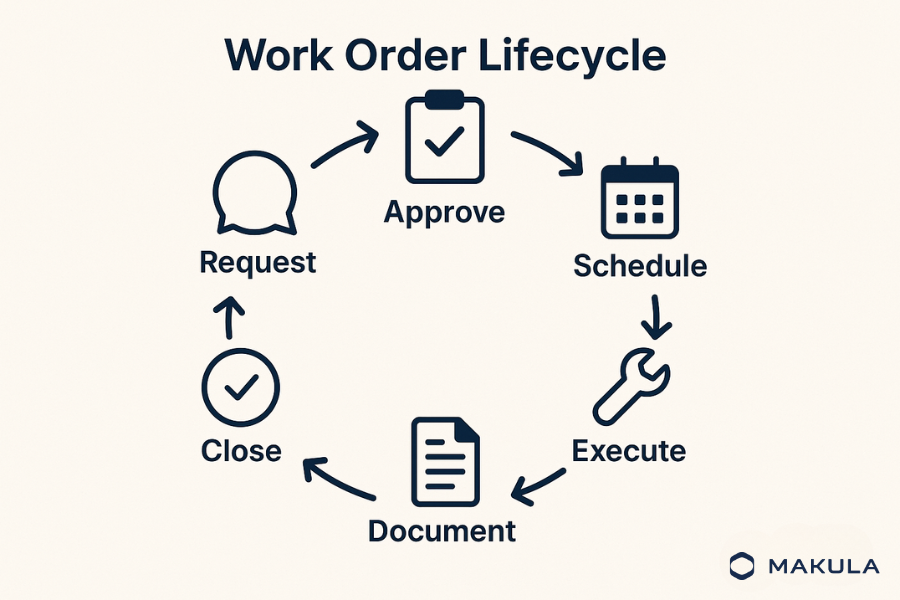
Work orders can be preventive (scheduled checks), reactive (emergency fixes), or corrective (non-urgent repairs). The right system helps teams prioritise, respond, and analyse work in a structured, auditable way.
3. Why Digitising Work Order Management Is Crucial
Paper-based systems don’t just slow teams down—they actively introduce risk. Digitising work order management offers a measurable leap in efficiency, accountability, and asset longevity.
Key benefits:
- Real-time visibility: Managers and technicians always know what’s been done, what’s in progress, and what’s overdue.
- Mobile access: With apps like Makula Field Service and Makula CMMS, technicians can update job status, log parts, and attach photos from any location—online or offline.
- Automated scheduling: Trigger work orders from IoT sensors, preventive schedules, or SLA timers.
- Regulatory compliance: Digital records ensure you’re always audit-ready with safety and service history logs.
Ultimately, digitisation gives industrial teams control and foresight—helping them shift from firefighting to planned, data-informed execution.
4. OEM vs Factory Work Order Workflows: What’s the Difference?
The way work orders function in an OEM’s field service team is fundamentally different from how they’re managed on a factory floor. Understanding both is key to choosing the right system.
OEM Field Service:
- Work orders triggered by customer requests, IoT alerts, or SLA schedules
- Technicians dispatched off-site, with route optimisation
- Customer sign-off and feedback essential
- SLA penalties and customer satisfaction at stake
Factory CMMS:
- Work orders triggered by asset breakdowns, PM schedules, or operator reports
- On-site maintenance teams respond within the plant
- Prioritisation based on production impact and safety
- Documentation focused on audits, analytics, and asset history
5. Top Digital Work Order Tools in 2025
If you're comparing digital platforms, here are some top-ranked tools for modern maintenance and field service:
- ServiceNow FSM – Enterprise-grade, ideal for SLA-intensive service teams.
- IBM Maximo – Full-featured EAM for global maintenance operations.
- Fiix CMMS – Cloud-native with a strong UX for mid-market factories.
- Limble CMMS – Intuitive and highly customisable for small to mid-size operations.
- UpKeep – A technician-first mobile app designed for ease of use.
6. Why Makula Is Purpose-Built for OEMs and Factories
Makula isn’t just a maintenance tool. It’s a complete work order management engine with tailored solutions for both field teams and factory technicians.
Makula Field Service (for OEMs):
- Smart dispatch based on technician skills and geography
- SLA tracking and automated notifications
- Offline mobile access, with photo upload and signature capture
- Integrated with Customer Portal and Installed Base
Makula CMMS (for factories):
- Preventive work order generation
- Drag-and-drop maintenance scheduling
- Real-time analytics on downtime, cost, MTTR
- Audit-ready logs for compliance
Explore Makula Field Service | Explore Makula CMMS
7. How to Choose the Right Work Order Platform
Start by identifying your primary needs:
- Are you dispatching technicians to customer sites?
- Are you managing internal maintenance and asset uptime?
- Do you need SLA enforcement, predictive triggers, or regulatory audit logs?
Key criteria to assess:
- Integration with ERP, IoT, or CRM systems
- Mobile-first UX with offline support
- Asset registry and hierarchy support
- Support for both external and internal workflows
Avoid bolt-on tools that only solve half the problem. Look for systems that unify field service and internal maintenance where needed.
8. Why Makula Is the Best Choice in 2025
Makula offers a rare blend of field service flexibility and internal asset control. Whether you're maintaining thousands of factory assets or deploying service techs globally, Makula gives you:
- True dual-mode capability – CMMS for your plant and FSM for your customers
- Mobile-first tools – Offline-ready apps for any technician
- Smart scheduling and IoT readiness – Integrates with asset sensors and SLA timers
- Data-first design – Analytics, asset histories, and service feedback in one place
Makula isn’t trying to be everything to everyone—it’s purpose-built for factories, facilities and OEMs.