If you're managing field service for industrial equipment, you know the daily friction: technicians waste time searching for past job details, onboarding takes too long, and reports often get filled out hours after the fact, if at all.
Meanwhile, customers expect faster fixes, detailed documentation, and fewer repeat visits.
That’s where AI in field service comes in. It helps technicians access the right information in seconds, guides them step-by-step during complex repairs, and handles documentation automatically. This allows them to focus on the work, not the admin.
In this article, we’ll break down what field service AI is, how it works on real jobs, and how OEM teams are using it to save time, reduce errors, and scale faster.
What Is Field Service AI?
Field service AI uses artificial intelligence to support technicians during real jobs. These tools help field teams work faster, solve issues more accurately, and reduce manual tasks.
Here’s what field service AI can do:
- Suggest the right repair steps based on past jobs
- Pull up service history, manuals, and diagrams automatically
- Fill out notes and forms while the technician works
- Guide new technicians through each step in real time
- Give managers a clear view of asset history and field activity
- Capture team-wide knowledge to reduce reliance on senior staff
Unlike traditional service software, AI tools don’t rely on static checklists. They learn from real job data. The more your team uses them, the more helpful they become.
Many OEMs are already making the switch. 78% of high-performing field service teams already use AI-enhanced software to improve efficiency.
78% of high-performing field service teams already use AI-enhanced software.
Why OEM Field Service Teams Are Turning to AI
Customers now expect faster repairs, fewer delays, and a full record of every visit. But hitting those expectations is hard when:
- Technicians spend too much time filling out reports
- Senior team members carry most of the knowledge
- New hires take weeks or months to get up to speed
These gaps cost time, lead to errors, and create pressure on your experienced team members. The more complex the equipment, the harder it is to keep up.
That’s why more teams are making the shift. In fact, according to the 2025 State of Field Service Report by Geotab, 93% of field service companies have already started implementing AI.
How AI Works in Field Service Operations
Here’s how AI supports OEMs in their field service operations:
AI-Powered Knowledge Access
Technicians often lose time searching through old reports or asking someone what was done last time. AI-powered search removes that step by connecting to service logs, manuals, and scanned documents.
So, when a technician opens a job ticket, the system can:
- Pull past service records for the same equipment
- Display manuals, diagrams, and troubleshooting steps
- Highlight common failure points based on past jobs.
Even older PDFs or technical drawings become searchable using built-in text recognition. This way, technicians give the answers they need without calling the office.
Technician Assistance in the Field
During a job, technicians can be unsure what to do next. This slows down repairs and leads to guesswork or calls for help.
AI tools like Makula’s Machinery Assistant guide technicians in real time using data from the equipment they are working on. It walks the technician through each step, such as replacing a part, checking a pressure reading, or confirming a service schedule. Since it runs through Makula’s mobile app, technicians can follow the guidance on-site without stopping the job.
This type of AI in maintenance and support cuts repair time by 39%, and helps every technician follow the correct process, even with unfamiliar equipment.
Post-Job Reporting and Documentation
After the job, technicians have to write down what they did. The general practice is to do it once they return back to the office. This slows everything down and leads to missed details.
Makula’s AI Notetaker removes that load by capturing what happens during the job as the technician works. It listens to what’s said, tracks actions, and fills out the service record in real time. If any details are missing, it flags them automatically and saves everything in a clear, searchable format.
Benefits of AI in Field Service for OEMs
Let’s take a look at the benefits of AI in field operations.
Faster Time-to-Resolution
Technicians often lose time searching for repair steps, manuals, or equipment history. Each delay adds time to the job and lowers team capacity.
AI tools solve this by surfacing the right information as soon as the technician opens the job ticket. They pull service logs, failure patterns, and steps that worked before.
Improved First-Time Fix Rates
When a technician shows up unprepared or missing parts, the job usually gets rescheduled. These repeat visits cost money and frustrate customers.
With AI, technicians get a full job brief before they arrive. It includes past issues, likely causes, and steps to take first. During the job, AI assistants support them with live guidance if anything changes.
This helps resolve the issue on the first visit. In fact, 75% of AI adopters report better first-time fix rates.
Reduced Technician Onboarding Time
New technicians need weeks to get up to speed. They don’t know the equipment, are unsure of the steps, and keep asking senior techs for help. This affects efficiency and takes time away from your more experienced staff.
Conversational AI in manufacturing helps close these gaps. It answers questions on the spot, walks new techs through the job, and shows what worked on similar issues before. This helps them learn faster, work on their own, and keeps senior staff focused on more important tasks.
Scalable, Consistent Documentation
When service logs are missing or messy, it’s hard to see what was done before. This can lead to repeated mistakes or problems during audits and warranty claims.
AI Notetakers fix this by recording what happens during the job. Powered by generative AI for the manufacturing industry, they track each step, fill in missing info, and build the report while the technician works.
Lower Operational Costs
Service teams lose time and money through rework, unnecessary travel, and admin overhead. When the right steps are unclear, mistakes and delays become common.
AI tools reduce these costs by helping technicians do the job right the first time, spend less time on reports, and avoid back-and-forth with the office.
According to Geotab, 88% of field service teams adapting AI report lower service costs.
Common Use Cases for Field Service AI
Here are some examples of AI in field service that support real OEM service operations.
Pre-Job Planning with AI Briefs
Before a technician arrives at a job, they often don’t know the full issue. Service history might be buried in emails, or no one remembers the last fix.
With AI enterprise search, a technician can understand service history before heading out. It includes past service logs, typical failure points, and the parts most likely needed. This saves prep time, reduces guesswork, and helps them bring what’s required.
In-Field Support During Complex Repairs
If a technician is working on a machine they’ve never handled before, they might stop to call someone or search through a manual.
With an AI assistant, they can instantly access that machine’s service history. It can walk them through the task step by step and suggest what to check based on past fixes.
This helps them stay focused, avoid delays, and complete the job without needing help.
AI-Powered Reporting at Closeout
According to Salesforce, field technicians lose over seven hours each week to tasks like writing notes, filling out forms, and updating records.
With AI tools, that step becomes faster and more consistent. The technician starts a voice recording during or after the job. The AI then transcribes and summarizes those notes into a structured report. It captures key actions, highlights missing details, and stores everything in a searchable format.
Remote Fault Detection and Dispatch
When a customer reports an issue with an injection molding machine, the support team doesn’t need to send someone on-site right away.
Instead, they use AI tools that:
- Analyze live sensor data from the machine
- Compare it with past service logs
- Flag the likely issue (for example, a worn hydraulic seal)
- Recommend a fix and which part to bring.
This way, the technician arrives with the right part, confirms the issue, and completes the fix in one visit.
Best Practices for Implementing Field Service AI
To get real results from AI in field service, OEMs need more than just tools. Here’s how OEMs can use AI in service the right way:
- Pick one clear starting point: Start where your teams lose the most time, like filling out reports or searching for repair history. These are quick wins with visible impact.
- Run a small pilot before scaling: Choose one equipment type or one service territory. Let real techs try AI tools on the job, then track results before scaling.
- Clean and organize your service data: Scan old manuals and handwritten logs, then digitize your field service operations. This helps AI tools access everything in one structured, searchable system.
- Train field and office teams together: Bring technicians and managers into the same sessions. Show how AI tools help them finish faster. Use their feedback to fine-tune the rollout.
- Track real outcomes: Check if time-to-resolution is going down. Are more jobs closed in one visit? Are techs spending less time on admin? Use this to improve.
Field Service AI Trends to Watch Out for in 2025
Field service automation with AI is advancing quickly. These trends show how OEMs can simplify workflows, reduce admin steps, and improve job support in the field.
AI Agents for Dispatch and Support
AI can assign tickets to the right technician by checking skills, location, and availability. It can also respond to customers with updates and schedule confirmations automatically.
Wearables and Augmented Reality
With smart glasses, a technician can view annotated diagrams or step-by-step video guides directly in their field of vision while working.
So, instead of pausing to check a tablet or call for help, they stay focused on the repair.
Generative AI for Job Briefs and Reports
AI creates pre-job briefs using service logs and writes post-job summaries based on technician input. This lowers admin time and keeps records consistent.
OEM-Specific AI Tools
Generic field service platforms give general checklists. But they don’t account for your machine’s unique failure patterns, part layouts, or service history.
Makula connects to your own documents, logs, and manuals. So when a technician opens a job, they get instructions tailored to that exact equipment model, including the fault type and the steps that worked in the past.
This also helps retain valuable service knowledge even as your workforce changes.
Makula’s AI Platform: Built for OEM Field Teams
Each tool in Makula’s platform solves a specific challenge that slows down your field service operations. Here’s how.
AI Notetaker for Hands-Free Documentation
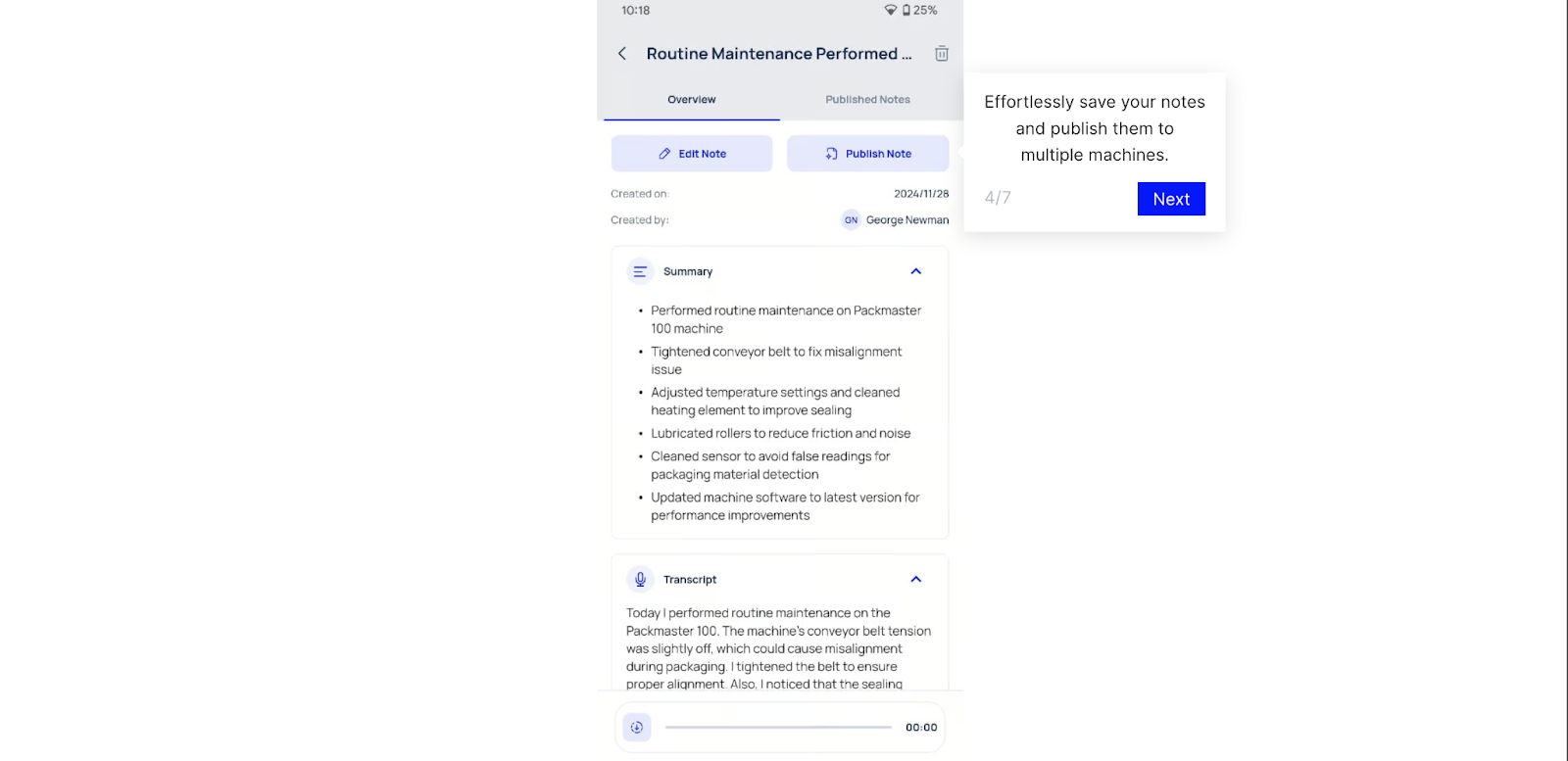
Writing reports after each job slows down closeouts and leads to missed info. Instead of stopping to type, the technician can use AI Notetaker to:
- Record voice notes during or after the job
- Get instant transcripts and AI summaries
- Store everything in one place, ready to review.
This speeds up closeouts and gives managers a clear, searchable record of what happened.
AI Search for Instant Knowledge Access
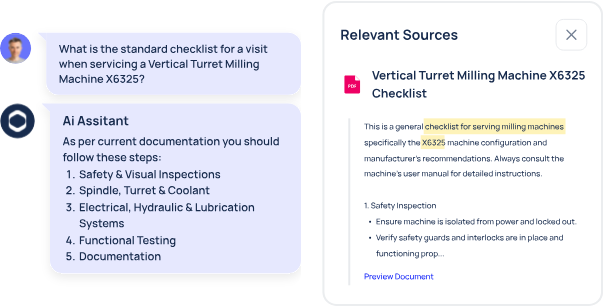
When a technician reaches a machine they haven’t worked on before, they open the AI Search tool in Makula’s app. They enter the asset ID or scan a barcode.
Here’s what shows up in seconds:
- The last three service logs for that exact model
- Wiring diagrams from the original manual
- A list of the top three fault codes linked to this machine
- The repair method that worked last time for this same issue.
This lets the technician skip guesswork, avoid calling someone, and fix the problem on the spot using verified steps that match the exact equipment.
Machinery Assistant for Onboarding and Troubleshooting
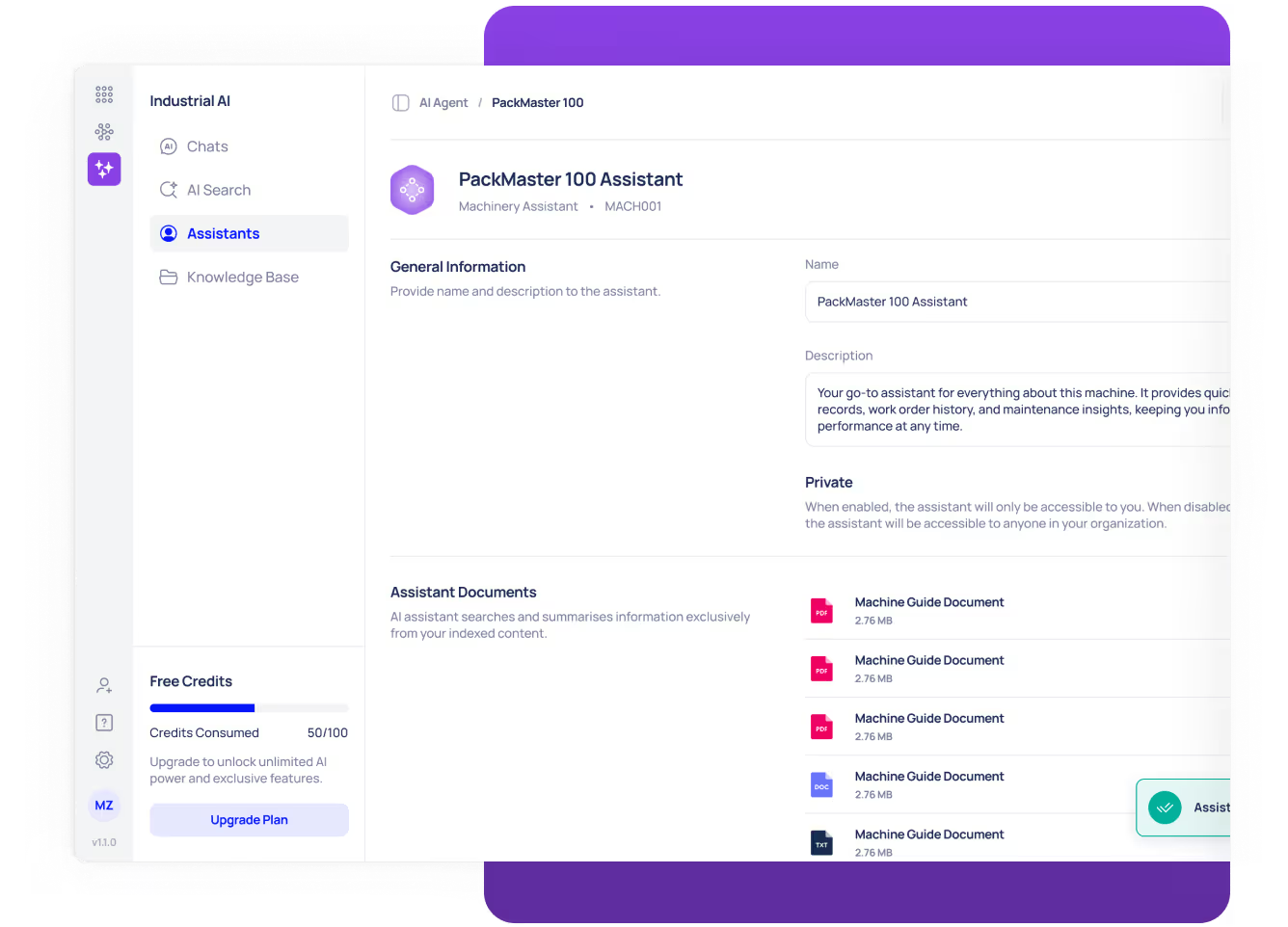
New technicians often pause mid-task because they are unsure what to do next. Makula’s Machinery Assistant acts like a guide by pulling instructions, diagrams, and service tips based on the specific machine in front of them.
It shows what usually fails, what to inspect first, and how others fixed the same issue. All of this appears on their phone while they work, so they stay focused and keep moving. This builds confidence, speeds up onboarding, and keeps senior staff focused on higher-priority work.
Struggling with slow ramp-up or repeat jobs? Book a demo to see how Makula’s AI in field service helps new techs work faster, fix issues right the first time, and reduce cost.