If you’re a maintenance manager relying on spreadsheets or paper checklists for equipment upkeep, you risk missed tasks, unplanned downtime, and rising costs.
According to data, 68% of plants experience unplanned outages at least once a month, with costs averaging $125,000 per hour.
That’s where equipment preventive maintenance software comes in. It automates schedules, work orders, inventory management, and reporting, all in one centralised platform.
In this article, we will review the 7 best equipment preventive maintenance software in 2025, so you can choose the right one for your business needs.
What is Equipment Preventive Maintenance Software?
Equipment preventive maintenance software is a type of computerised maintenance management system (CMMS) designed to streamline and automate scheduled maintenance activities.
By bringing maintenance planning and tracking into a digital platform, it reduces manual tasks and helps organisations stay ahead of equipment failures.
CMMS preventive maintenance features include:
- Automated preventive maintenance scheduling
- Work order management
- Real-time monitoring of equipment status, location, and performance
- Inventory management for spare parts and supplies
- Condition monitoring through IoT sensors and analytics
- Reporting and analytics for data-driven decision making
Manufacturing, energy and utilities, and food and beverage companies rely on preventive maintenance software to maximise equipment uptime, maintain compliance, and control costs in demanding environments.
8 Best Equipment Preventive Maintenance Software in 2025
Here is a breakdown of the seven best equipment maintenance software solutions:
Makula
Best for: Factories that want modern, AI-augmented CMMS for preventive maintenance and audit-ready workflows
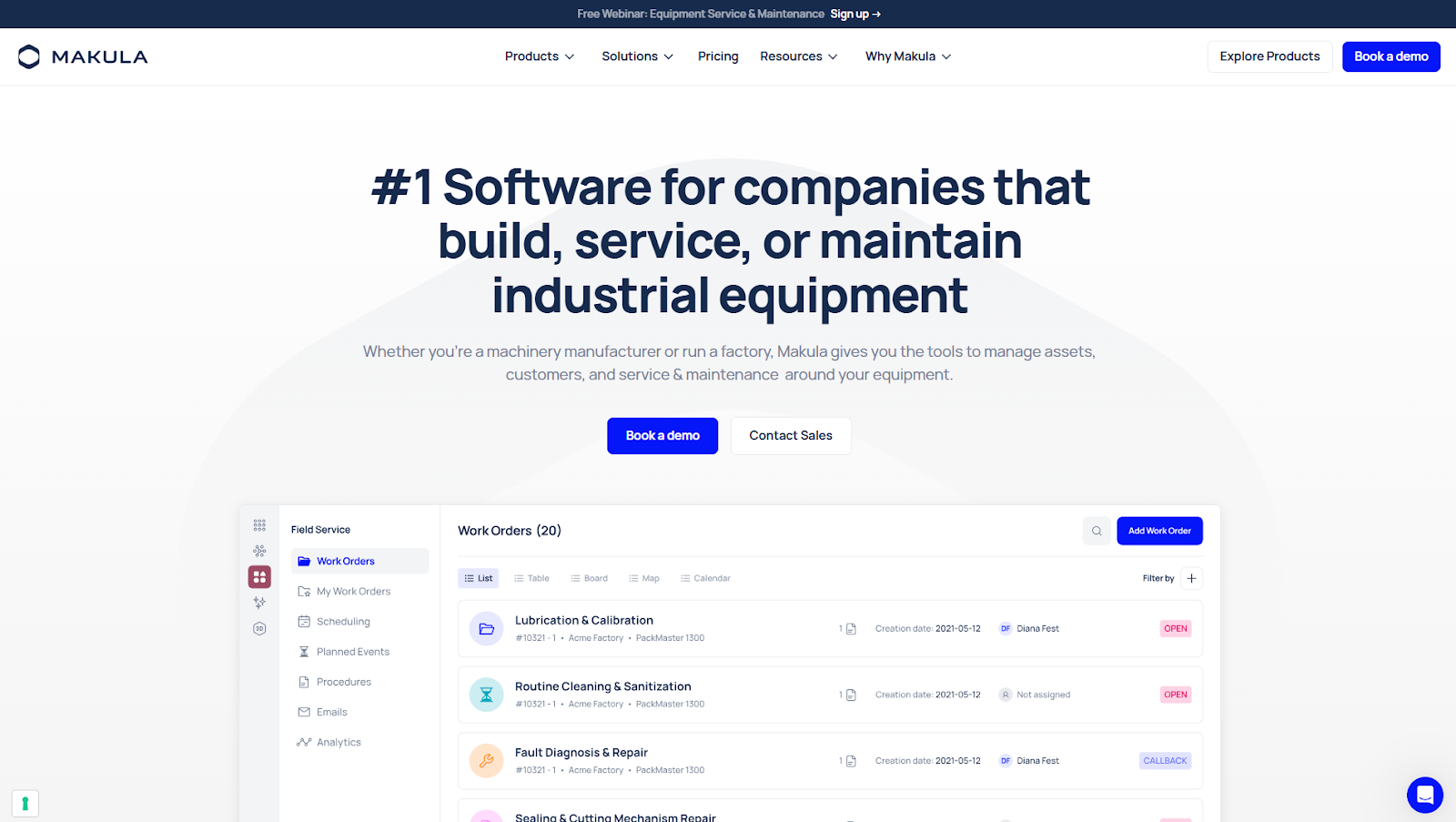
Makula is a modern computerised maintenance management system (CMMS) designed for maintenance and plant managers in asset-intensive industries who need reliable equipment performance.
Instead of relying on generic tools, Makula gives you automated inspections, precise maintenance scheduling, and real-time asset monitoring to reduce the risk of unexpected failures.
The platform offers a unified dashboard for scheduling, work order assignment, inventory control, audit-ready documentation, and actionable reporting.
Here are some of the core features that make Makula a top choice for preventive maintenance:
Automated Scheduling for Reduced Machine Downtime
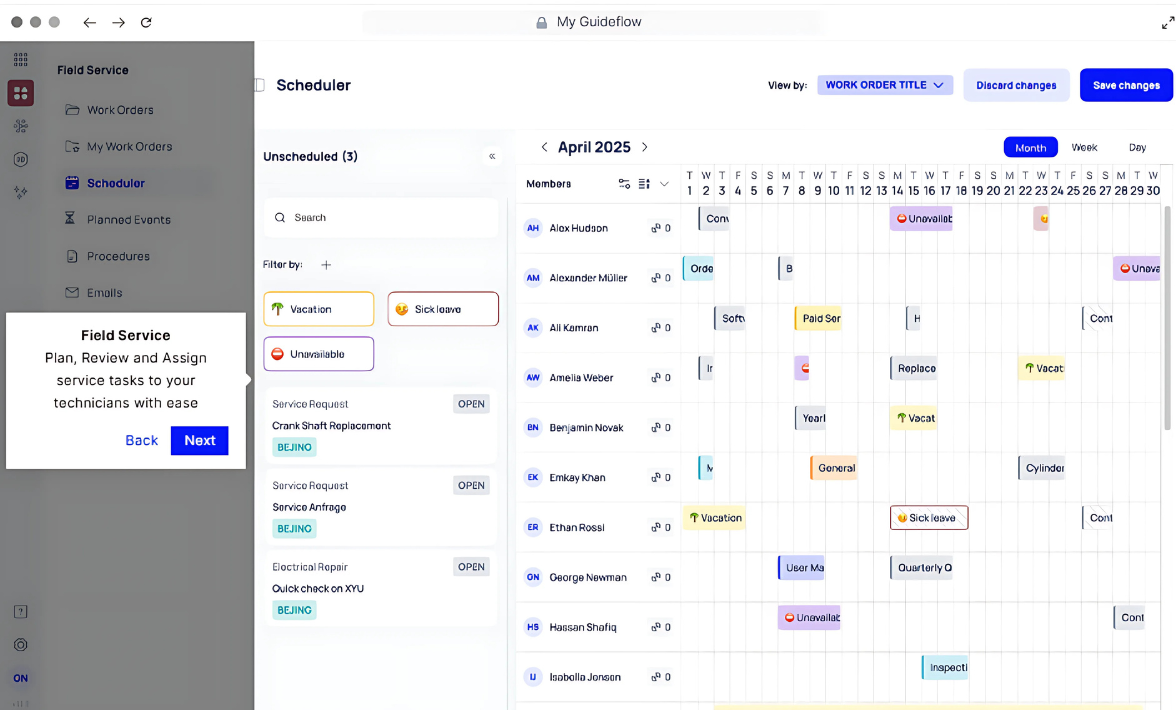
Missed service tasks can lead to equipment failures and costly downtime, especially when schedules and staff availability are tracked in multiple places or assigned by memory.
Makula’s Scheduler puts all maintenance planning on one calendar. Here’s how it helps:
- See your team’s real-time availability to avoid double-booking.
- Schedule time-based maintenance at daily, weekly, or monthly intervals, with automatic reminders.
- Trigger tasks based on equipment usage, like hours or cycles.
- Assign jobs with a simple drag-and-drop onto the calendar.
- Filter out technicians on leave or unavailable to prevent conflicts.
- Reshuffle assignments easily when priorities or availability change.
For example, if your packaging line needs preventive maintenance every 5,000 cycles, Makula automatically tracks equipment usage, schedules the service as soon as the threshold is reached, and assigns it to an available, qualified technician, all without manual tracking or guesswork.
Work Order Management for Efficient Task Execution
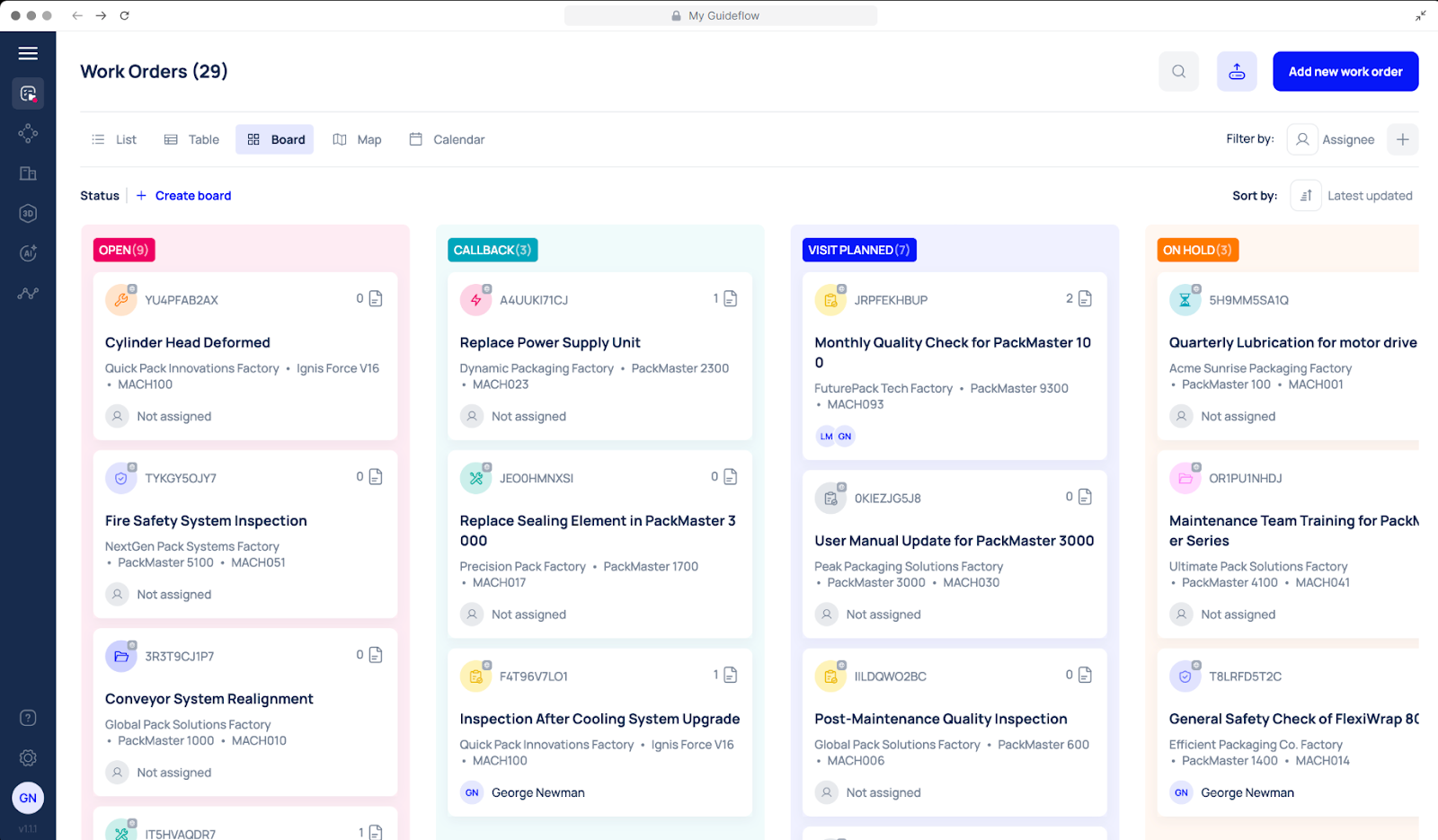
Maintenance teams lose time and miss details when work instructions are spread across emails, paperwork, or disconnected systems. This creates unclear priorities and the risk of incomplete jobs, impacting production.
Makula centralises all work orders through a work order management system, making it easy to initiate, assign, and track every maintenance task from start to finish.
Here’s how Makula supports your maintenance process:
- Easy creation and assignment: Launch new tasks in seconds and direct them to the right technician with instructions
- Clear checklists and procedures: Attach step-by-step guides to make sure technicians have everything they need at the job site
- Integrated communication: Notes, emails, and chat keep the whole team connected without switching apps
- Accurate documentation: Use pre-filled templates, required fields, and digital signatures to capture complete records for every task
For example, if a production line motor requires urgent attention, you can open a work order, attach the right checklist, and select an available technician. As the task progresses, supervisors and team members track status live on the Kanban board and see key metrics update automatically.
Mobile-friendly Checklists for On-site Compliance
Paper checklists make it easy to overlook steps, misread notes, or lose important compliance records. This slows down audits and causes critical issues to be ignored on the plant floor.
Makula solves this by bringing structured, digital checklists to every technician’s mobile device. Each inspection is guided, step-by-step, with clear instructions and required fields to ensure nothing is left out.
Here’s how Makula’s mobile checklists work in practice:
- Structured forms: Clear, step-by-step instructions ensure inspections are complete and consistent.
- Offline and media-ready: Technicians can work without the internet and attach photos or signatures as proof.
- Automated scheduling: Tasks are assigned and reminded automatically to prevent delays.
- Audit trail: Every checklist is timestamped, linked to assets, and logged with supporting media for compliance.
- Centralized records: All data is stored in one searchable system, organized by asset, date, technician, or location.
For example, if a technician performs a lubrication check on the packaging line, they can use Makula’s mobile checklist to follow each step, attach a photo of any issue, and submit results right from the shop floor. All activity is instantly logged and supervisors are notified for follow-up and compliance.
Asset Tracking for Better Maintenance Planning
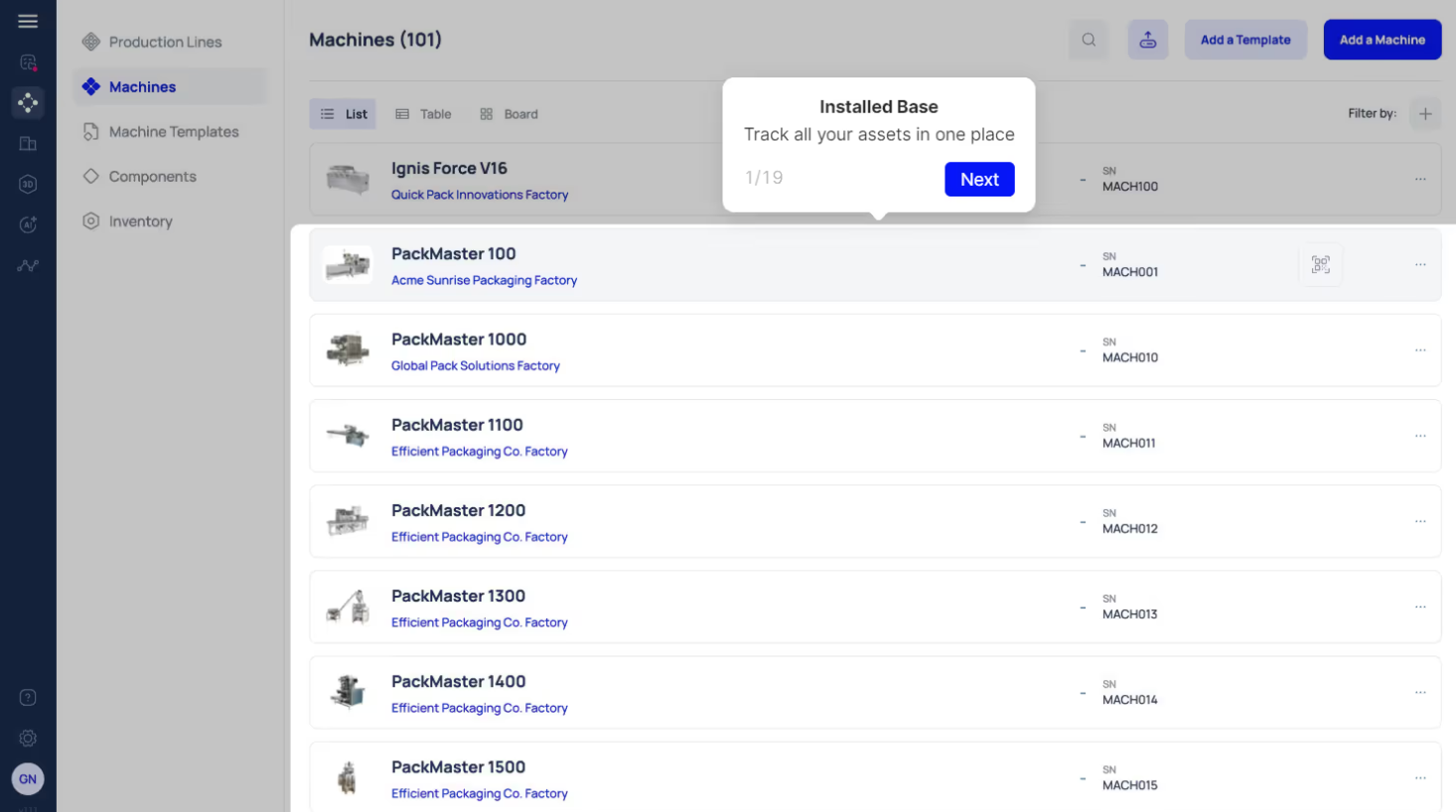
Unplanned breakdowns and costly downtime happen when you wait for equipment to fail. This reactive approach raises repair costs, disrupts production, and strains critical assets.
Makula’s Asset Hub lets you monitor every asset’s status and maintenance needs in real time. With all equipment tracked and its service history visible, you can prevent failures before they happen and make smarter, data-driven maintenance decisions.
How Makula’s asset tracking helps your operation:
- Real-time asset monitoring: IoT sensors and smart tracking reveal which machines are overworked, trending toward failure, or due for service
- Automatic PM triggers: Usage data and condition monitoring feed directly into your preventive maintenance plan, so service is timed precisely.
- Inventory and lifecycle insights: By linking asset data to inventory and maintenance schedules, you avoid costly rush orders, reduce unnecessary stock, and support smarter capital planning
- Centralised access: All asset details, from manuals to compliance certificates, are just a QR code scan away, giving your team instant answers and faster troubleshooting
For example, if a key compressor starts to show wear, Makula alerts the team before downtime hits. The maintenance manager can review the full service history, schedule repairs, and instantly access records for audits.
Real-time Reporting for Continuous Improvement
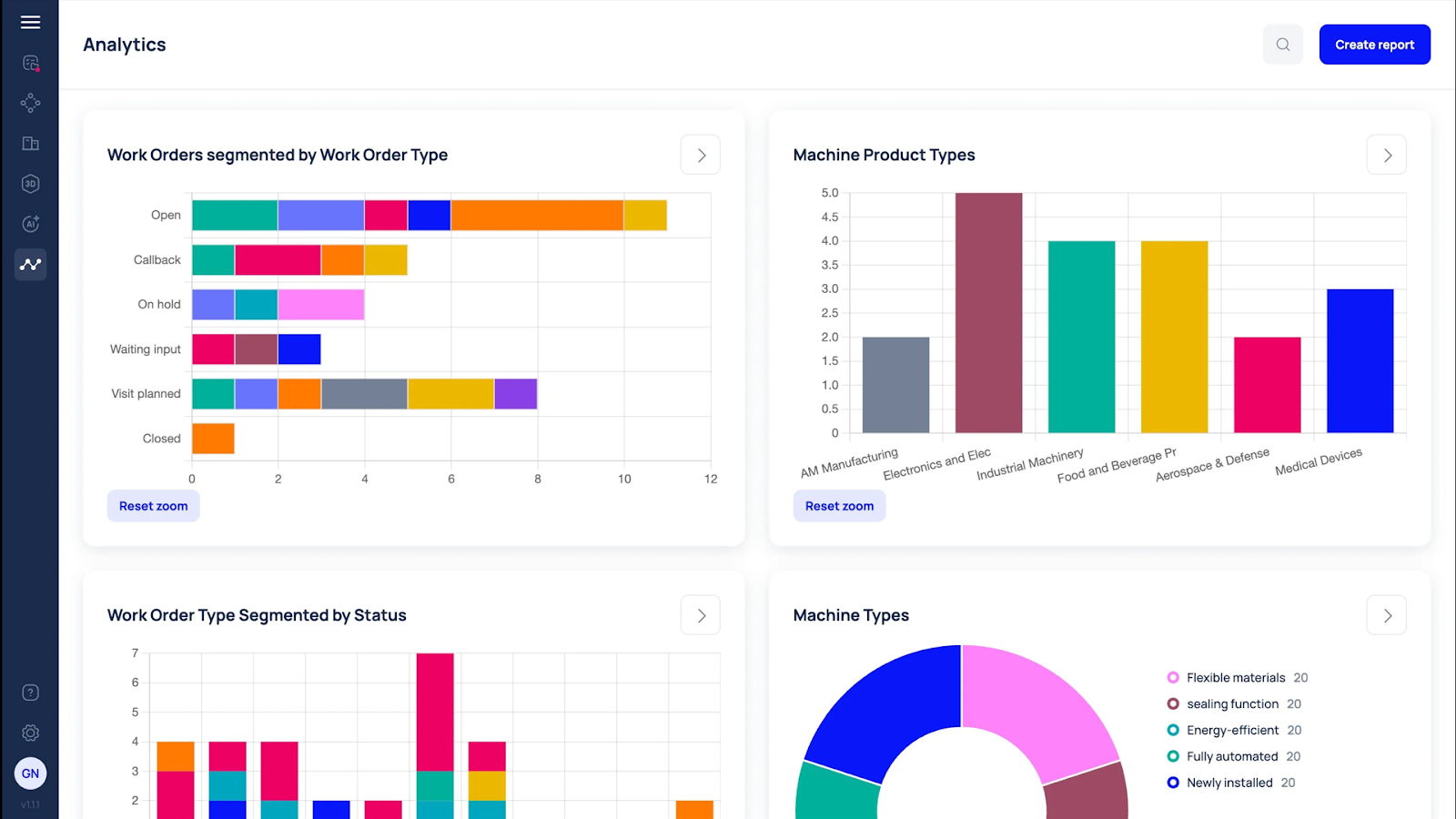
Audits become stressful when there’s no clear record of what has been done, and managers are under constant pressure to boost uptime and maximise the performance of every asset.
With Makula’s analytics capabilities, you get the insights needed to break this cycle. Real-time maintenance data lets you track failures as they happen, spot trends early, and back every decision with hard evidence.
You can create customizable reports for work orders, assets, and connections. Flexible filters, interactive drilldowns, and multiple chart types help you visualise what’s happening across your operations.
You can choose from five chart types:
- Table Chart
- Vertical Bar Chart
- Horizontal Bar Chart
- Pie Chart
- Number Chart
You can filter any report by asset, team, or shift to find trends, identify recurring failures, and see how your preventive maintenance changes are working. This helps you answer auditor questions, reduce costs, and increase productivity and ROI.
AI Copilot for Instant Guidance and Knowledge Capture
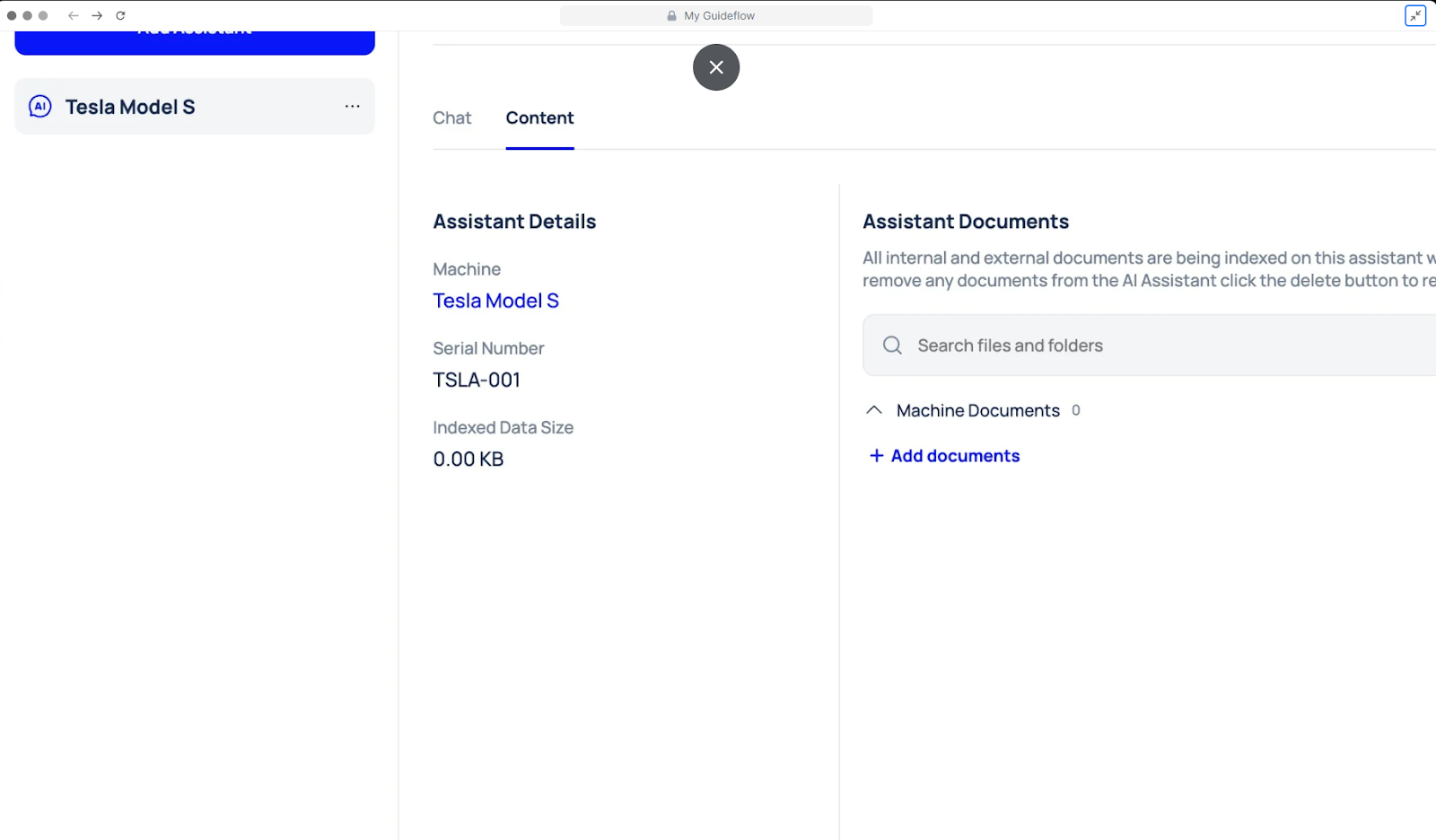
In many manufacturing facilities, critical maintenance knowledge is often locked away in manuals, hidden in service records, or stored only in the minds of a few experienced technicians.
Makula’s AI Copilot acts as a digital maintenance assistant for every asset you operate. It delivers instant, expert-level answers by pulling from your documents and machine files, making the knowledge you already have instantly accessible, with clear citations.
For example, during a line stoppage, a technician can simply scan the asset’s QR code, ask AI Copilot for troubleshooting advice, and receive instant guidance based on the machine’s history and documentation. There’s no need to wait for an expert or search through old files.
Book a free demo and learn how Makula can help you stay on top of preventive maintenance.
Makula Pros and Cons
Pros
- Helps shift teams from reactive to proactive maintenance culture
- Supports continuous improvement with data-driven insights
- Improves regulatory compliance by maintaining consistent records
- Reduces emergency repair frequency, saving time and costs
- Enhances the reliability and lifespan of critical assets
- Promotes accountability by making task progress visible to everyone
- Facilitates knowledge sharing so new team members can quickly get up to speed
Cons
- Occasional learning curve for teams new to digital maintenance tools
- Initial data setup can be time-consuming
Makula Pricing
Makula’s CMMS is available at €55 per user per month. Contact our team for more details.
Sockeye
Best for: Maintenance teams looking for an easier and faster way to track preventive maintenance
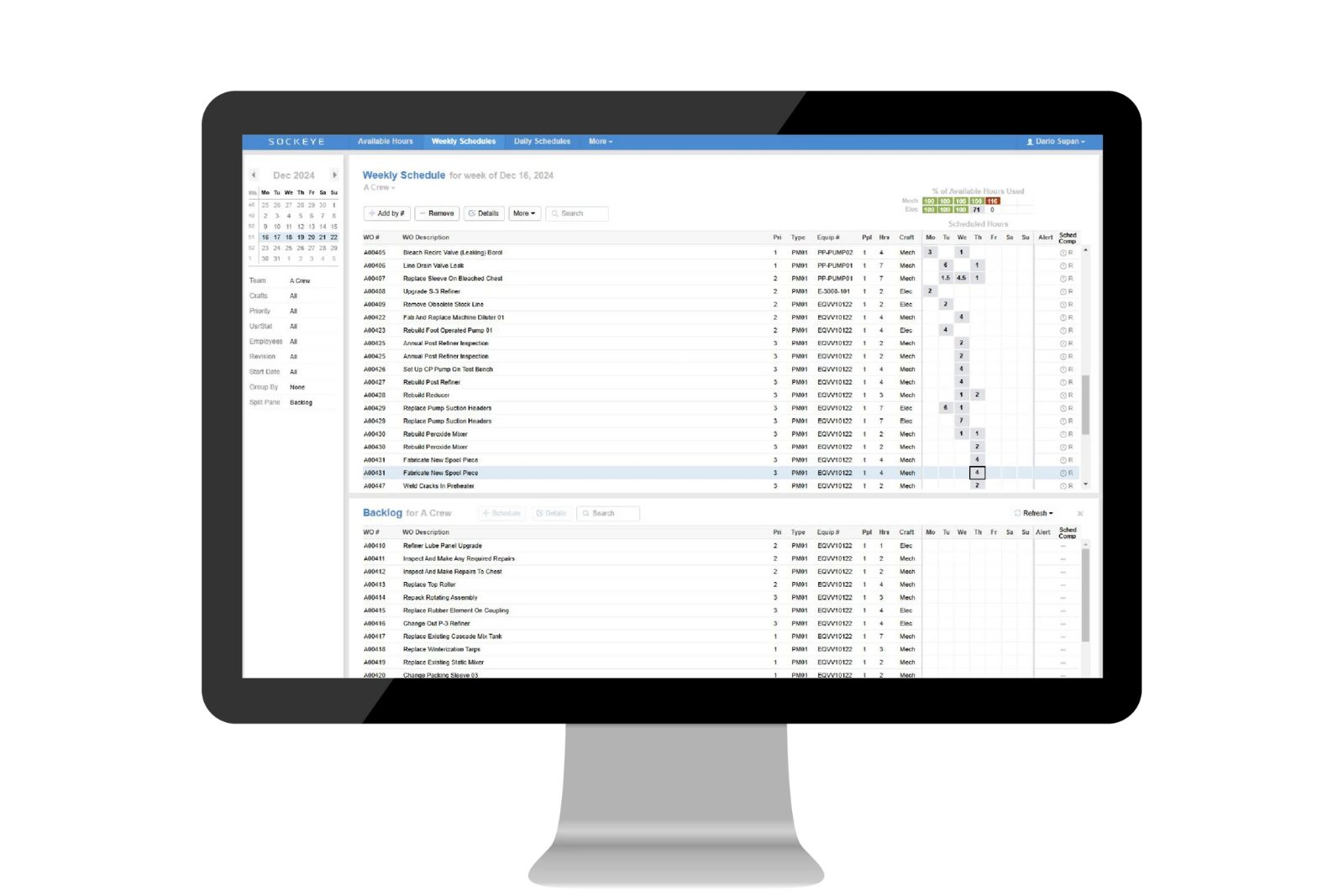
Sockeye is a cloud-based maintenance scheduling tool. It is built to bridge the gap between preventive maintenance plans and daily execution.
Instead of spending hours in updating and managing spreadsheets, Sockeye can help you create weekly or daily maintenance schedules in minutes.
To start with, it shows you exactly how much labor is available. It also helps in assigning tasks fairly, and lets the whole team see the plan in real time.
Companies using Sockeye have seen higher schedule completion rates, less overtime, and better equipment uptime.
Sockeye Key Features
- Make preventive maintenance schedules in minutes
- See available staff and balance workloads easily
- Works with popular CMMS/EAM systems like SAP and Maximo
- Track key stats like completion rates and backlog
- Secure cloud hosting with role-based access
- Simple drag-and-drop changes for last-minute work
Sockeye Pricing
Sockeye offers custom pricing. Contact the team for a quote.
Axxerion CMMS
Best for: Facility maintenance teams needing AI-powered, customizable preventive and predictive maintenance
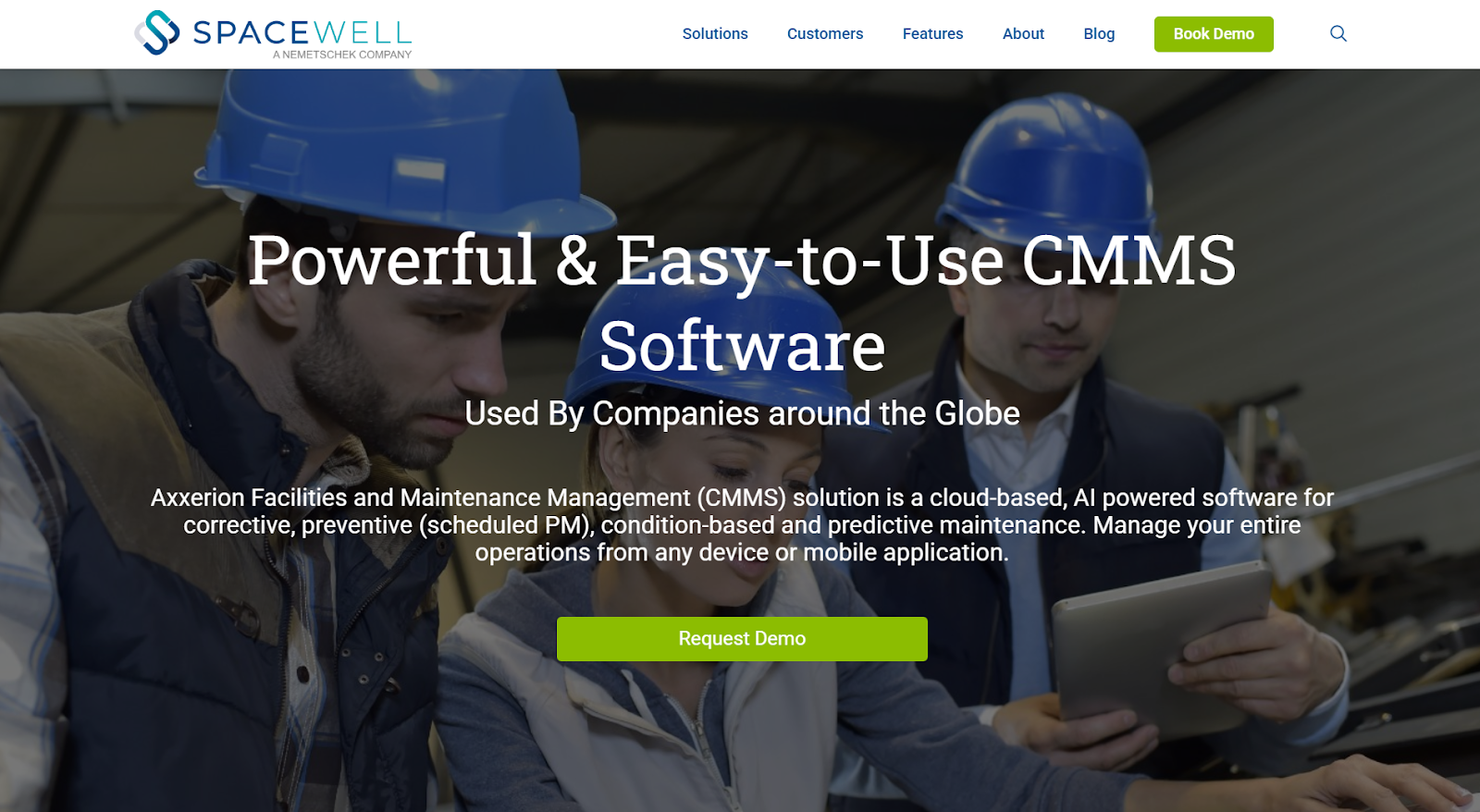
Axxerion Facilities and Maintenance Management (CMMS) is a cloud-based, AI-powered solution for corrective, preventive (scheduled PM), condition-based, and predictive maintenance. The platform lets you customise PM alerts, dashboards, and reports to fit your specific maintenance needs.
Axxerion Key Features
- Manage, schedule, and assign work orders
- Automate preventive maintenance
- Streamline Accounting and PO Invoicing
- Track assets with Enterprise Asset Management (EAM)
- Project Management (PPM) tools
- Real-time data with Reports & Dashboards
Pricing
Axxerion offers custom pricing. Contact their team for a quote.
Asset Panda
Best for: Construction, education, and asset-heavy teams requiring barcode tracking and unlimited users
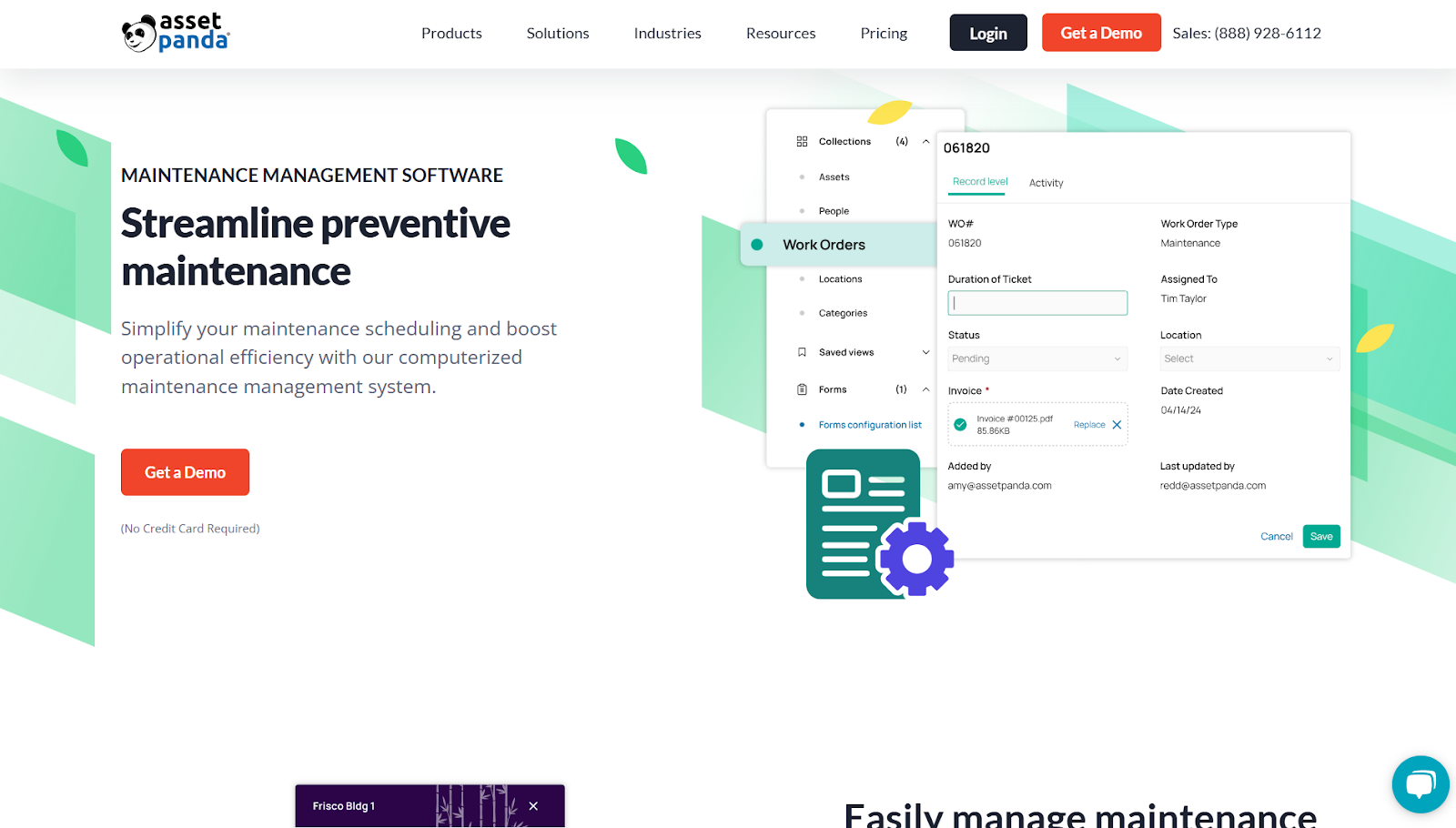
Asset Panda is a platform for asset management and preventive maintenance. Teams can automate PM schedules, assign tasks, and track work orders in real time. Pricing is based on the number of assets, with unlimited users supported.
Asset Panda Key Features
- Barcode and QR code asset tracking via mobile app
- Automated alerts and custom notifications
- Centralised asset records with maintenance history
- Mobile access for on-the-go task completion
- Digital documentation for compliance and audits
Asset Panda Pricing
Pricing is asset-based and includes unlimited users. Contact their team for a custom quote.
Eptura
Best for: Manufacturing teams, preventive scheduling and visual asset dashboards.
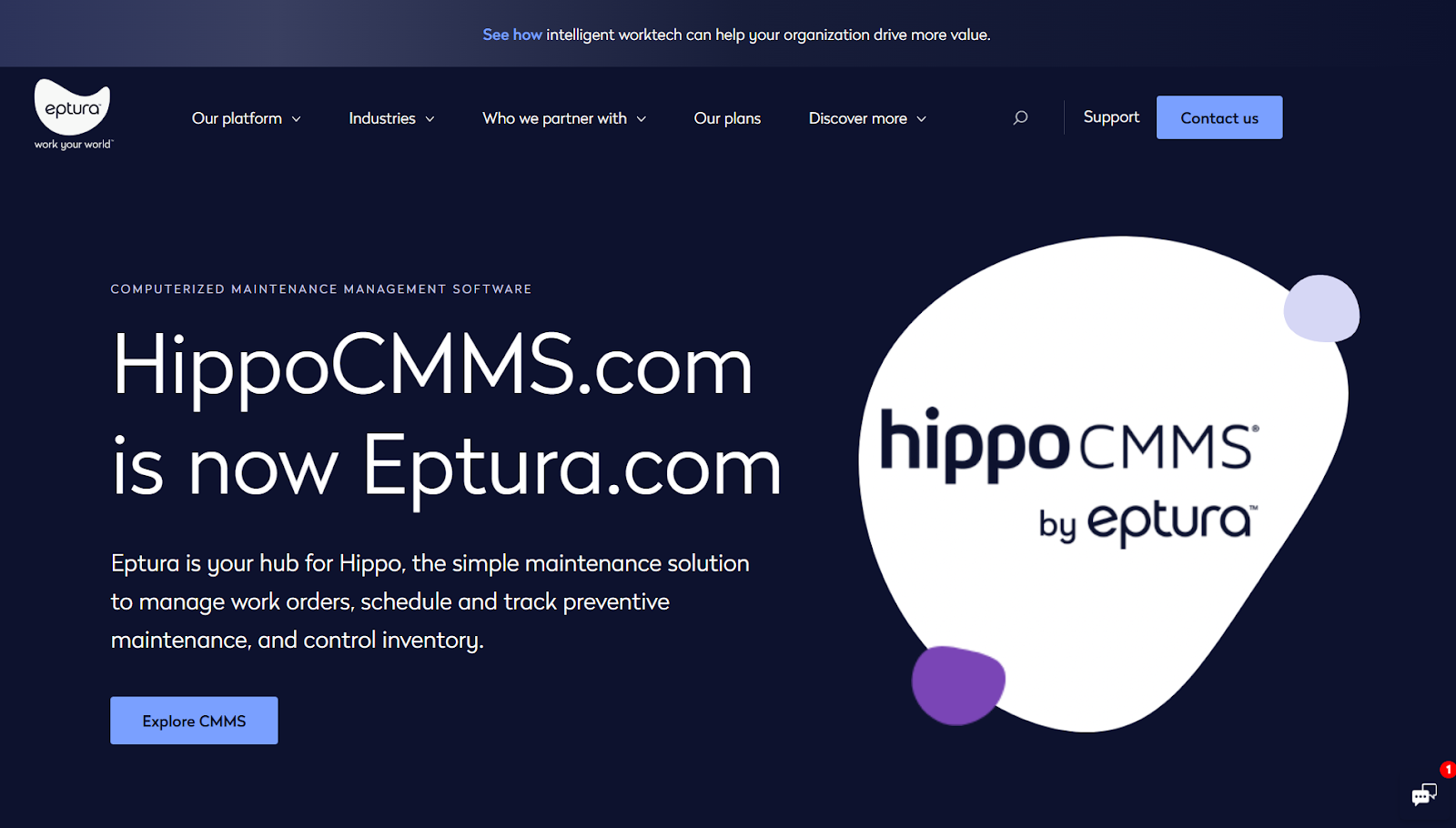
Eptura, previously known as Hippo CMMS, is a maintenance management platform built for facility and maintenance teams that need reliable preventive maintenance scheduling, work order tracking, and inventory management.
The system helps teams move from reactive fixes to proactive planning by making it easy to schedule recurring maintenance, manage work orders, and track asset performance.
Eptura Key Features
- Schedule and track preventive maintenance tasks
- Barcode and QR code scanning for easy asset tracking
- Visual equipment dashboard for real-time status updates
- Mobile access for technicians in the field
- Automated alerts and reminders
- Compliance-ready maintenance records
Eptura Pricing
Eptura is offered in two plans: Advanced and Power. Contact their team for a quote.
eMaint
Best for: Manufacturing, oil & gas, and audit-focused teams using advanced preventive maintenance triggers.
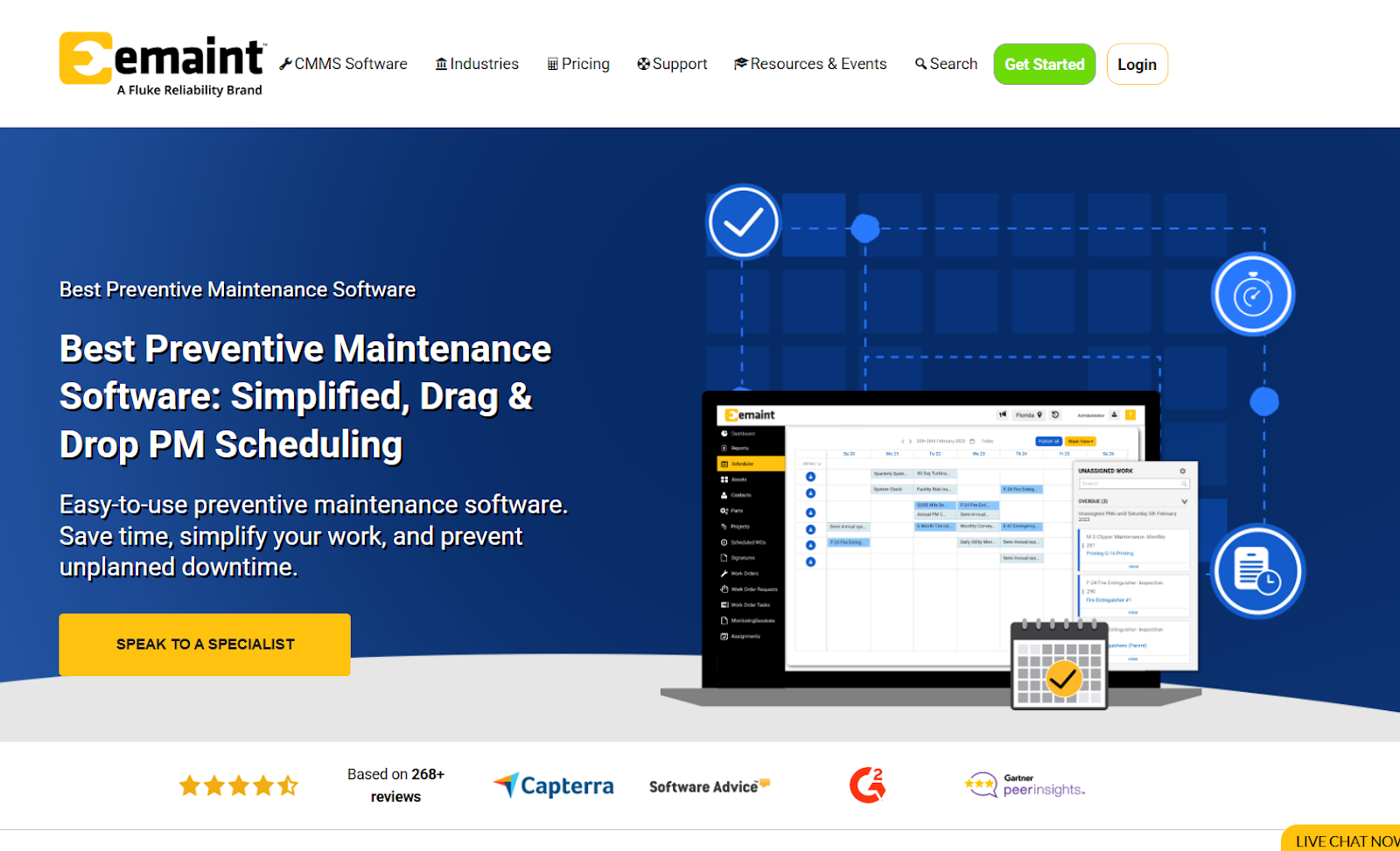
eMaint CMMS, backed by Fluke Reliability, is built to simplify preventive maintenance. It shifts teams from reactive firefighting to proactive asset management. Its intuitive PM scheduler lets you easily set time- or meter-based maintenance cycles with drag-and-drop.
eMaint Key Features
- Preventive maintenance with time- or usage-based scheduling
- Set up alerts and reminders for upcoming tasks
- Monitor PM compliance and completion rates
- Access step-by-step procedures and attach documentation
- Generate reports for audits and compliance
- Track maintenance costs and downtime metrics
eMaint Pricing
eMaint offers three plans: Team, Professional, and Enterprise.
Limble CMMS
Best for: Field service teams, mobile-first work orders and IoT asset tracking
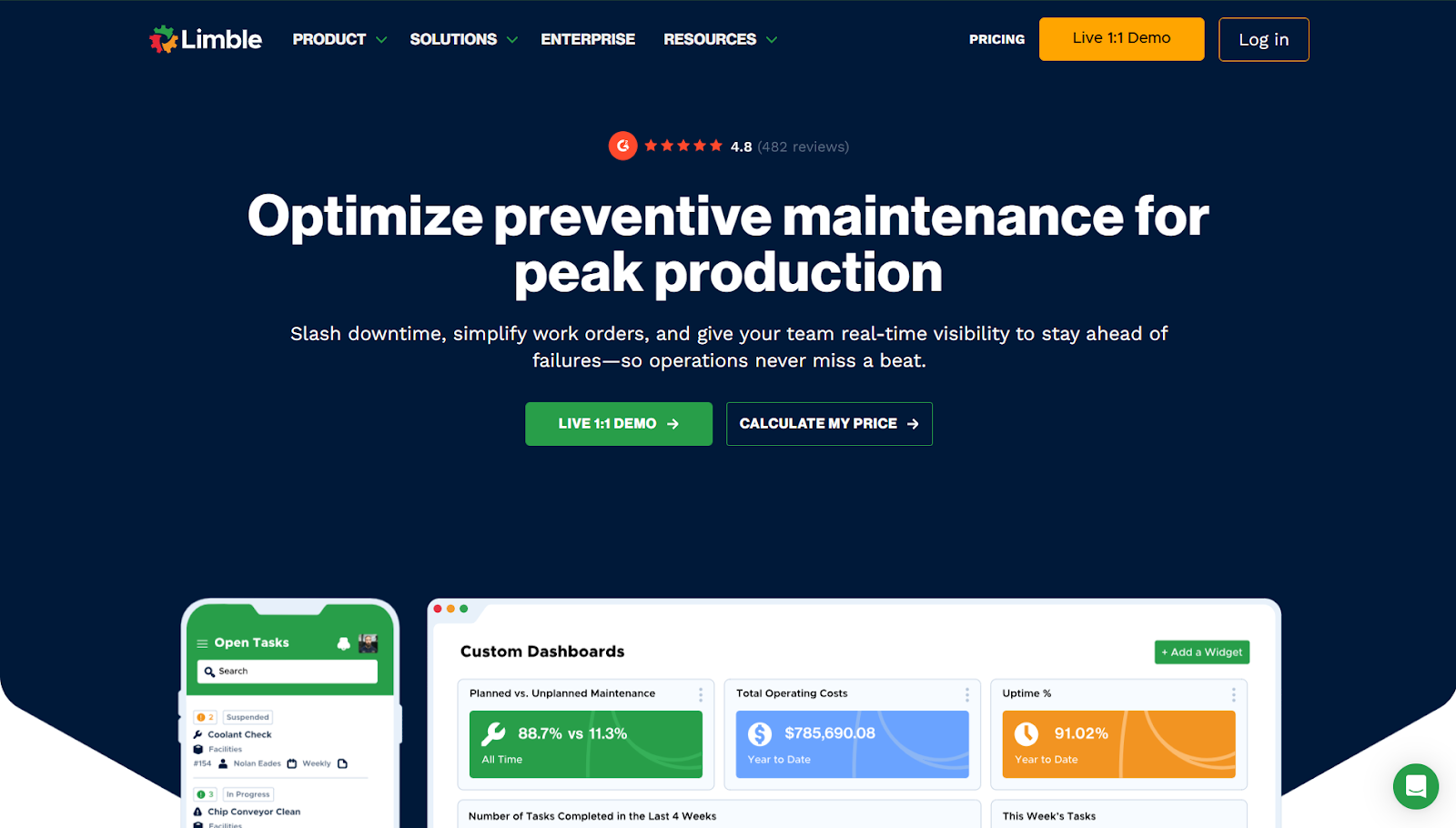
Limble CMMS is an asset management solution trusted by professionals for its ease of use and proactive maintenance approach.
Designed for technician-first workflows, Limble enables teams to automate preventive maintenance schedules, manage work orders, and track asset health, all from both desktop and mobile devices.
Limble CMMS Key Features
- QR code-enabled asset tracking and work order access
- Real-time dashboards to monitor maintenance KPIs
- Predictive maintenance with IoT sensor integration
- Automated alerts and reminders for upcoming tasks
- Track MTBF, downtime, and maintenance costs
Limble CMMS Pricing
Limble offers three tiered plans: Standard, Premium, and Enterprise.
FieldEx
Best for: Operations handling remote assets, sensor-based PM, and location-driven scheduling
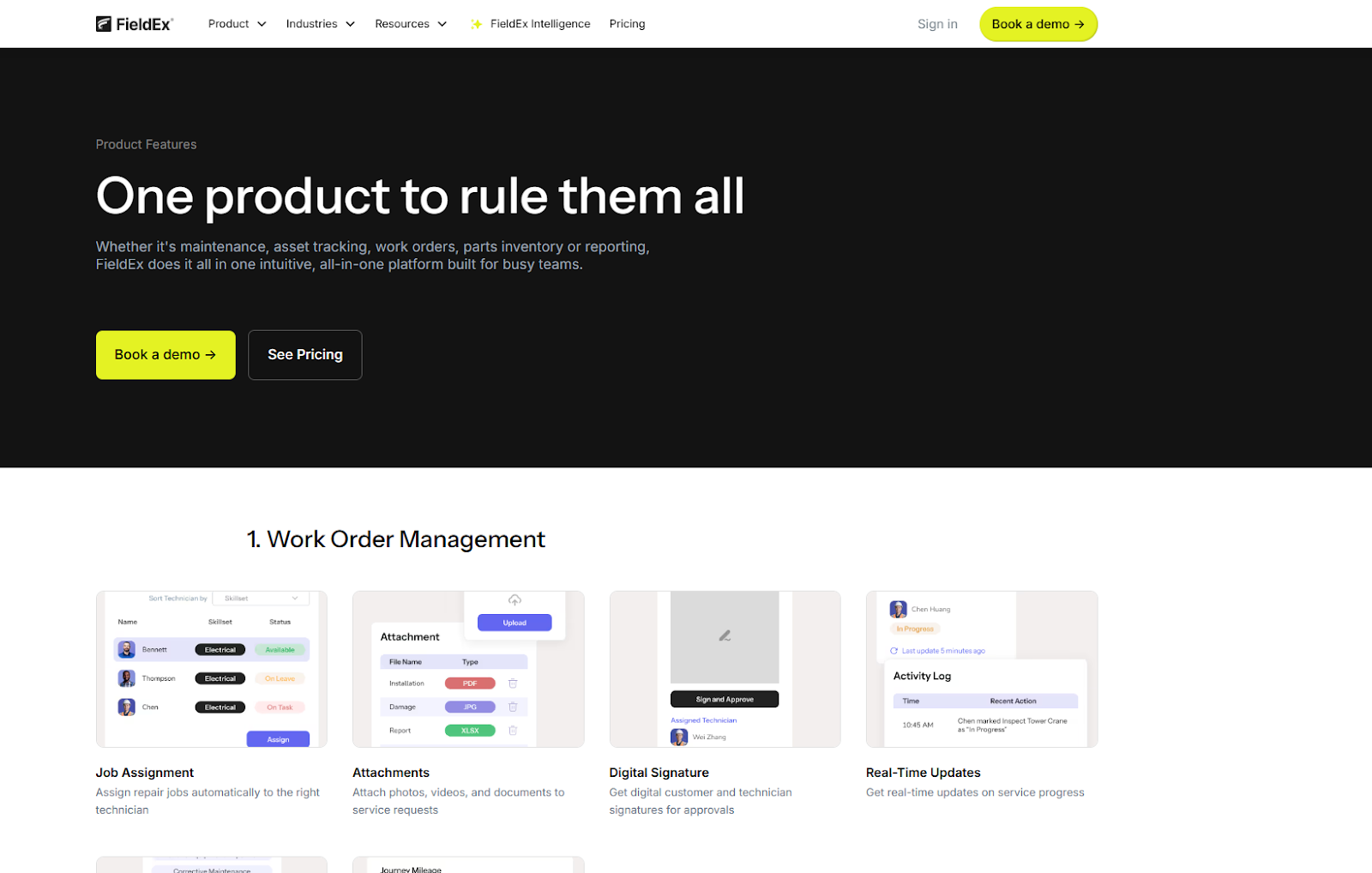
FieldEx stands out as a maintenance and field service platform built specifically for industries with distributed assets and mobile teams.
FieldEx prioritises field operations, offering preventive maintenance scheduling that accommodates the complexities of on-site and remote asset care. You can automate service routines not just by time or meter readings, but also using live sensor data and geolocation.
FieldEx Key Features
- PM templates for consistent tasks
- Auto-generate work orders
- Visual dashboard for task tracking
- IoT-based predictive maintenance
- Geolocation for smart dispatch
- Spare parts tracking
FieldEx Pricing
FieldEx offers four plans available: Lite, Growth, Pro, and Enterprise.
Comparison Table: 8 Best Equipment Preventive Maintenance Software in 2025
Benefits of Equipment Preventive Maintenance Software
Preventive maintenance helps manage equipment proactively by scheduling tasks and balancing workloads across assets. CMMS software makes it easier than ever to organise and automate these processes.
Less Unplanned Downtime
Unscheduled breakdowns slow production, create chaos, and drive up costs. With Makula’s automated work order generation and reminders, critical maintenance gets done right when it’s needed, so nothing slips through the cracks and your team stays ahead of failures.
Higher Team Productivity
When technicians have clear instructions and the right tools, tasks get done faster and with fewer mistakes. Makula streamlines this with mobile checklists and guided work orders, so your team can work efficiently and report issues from anywhere.
Easier Compliance and Audits
Passing audits and meeting regulatory requirements means keeping detailed, accurate records. Makula does this automatically, logging every maintenance action with time stamps, photos, and digital signatures.
Smarter Preventive Maintenance Decisions
Knowing what’s happening with your equipment lets you allocate resources wisely and adjust your preventive maintenance plan for better outcomes. Makula’s analytics feature make it easy to spot trends, get actionable recommendations, and focus your efforts where they’ll have the most impact.
Flexible Preventive Maintenance Scheduling
Every asset is different, and Makula gives you the flexibility to schedule maintenance by time, meter readings, or condition thresholds. You can tailor PM frequencies and prioritise tasks based on asset criticality.
Bottom Line: Improve Uptime and Cut Costs With Makula’s Equipment Preventive Maintenance Software
Unplanned downtime in asset-heavy industries leads to missed deadlines, rising repair costs, and lost revenue. Over time, these setbacks reduce equipment value, put compliance at risk, and hold back business growth.
Makula is built to break this cycle. With automated preventive maintenance, real-time reporting, and AI-powered recommendations, Makula gives maintenance teams the visibility and control needed to catch issues early and keep every asset performing at its best.
Book a free demo to see how Makula can help your team prevent costly downtime, lower maintenance expenses, and build a more reliable operation.