When you’re working with multiple active work orders across factories, it’s easy for things to slip. This means one missed update, coordinating high-stakes repairs, or a task assigned to the wrong technician can, over time, lead to delays, frustrated clients, and avoidable rework.
That’s why more OEMs are turning to field service management software. It gives you a smarter way to organise your field teams and respond faster when things go wrong.
Here’s how the right field service management platform can help:
- Track every work order from start to finish to keep your service operations clear, consistent, and on schedule
- Assign the right job to the right technician in real time
- Automate repetitive tasks to free up your engineers’ time
This article will share 7 successful tips to help you manage your field service engineers more effectively. It will discuss what works and how tools like Makula can support every step, from dispatch to debrief.
8 Expert Tips to Streamline Field Operations for OEMs
Here are 8 expert tips that will help you simplify the process of managing field operations across multiple factories and run a more efficient, responsive service team.
1. Schedule Work in Real Time
Real-time scheduling helps you assign the right technician to the right job without delay. With full visibility into team availability, you can match each task to the most qualified engineer and send them where they’re needed most.
For example, if a production line in one factory goes down, you can quickly dispatch the nearest technician with the right skill set, instead of waiting for someone to finish a less urgent job across town.
Makula makes this easy. You can view technician schedules, filter by skill, and assign work orders instantly, all in one place.
2. Optimise the Work Order Life Cycle
Managing work orders through a centralised system helps reduce delays and keeps everyone on the same page. When schedules, task details, and asset information are stored in one place, your teams can access what they need without manually chasing down files or updates.
For instance, when a technician completes a service call at a factory, the system can automatically trigger the next step, whether that’s a follow-up inspection or generating a service report for the client.
Makula lets you automate work order creation, assign tasks, and track progress through multiple visual views on its Work Order Board. This keeps your service operations organised, on time, and easy to manage.
3. Track Assets and Inventory
Delays often happen when technicians arrive on-site without the right tools or parts. That’s why it’s important to track inventory, equipment, and resource availability in real time across all locations.
For example, if a service call requires a specific diagnostic tool or replacement part, your system should show where it’s stored and whether it’s already in use. This avoids double-booking and keeps service running smoothly.
Makula lets you configure and assign limited resources like tools, vehicles, or testing equipment directly to work orders. This means your technicians have what they need, when they need it.
4. Use a Mobile Field Service App
When relying on spreadsheets or paper forms, your technicians lose time searching for job details, updating records, or calling back to confirm next steps. A mobile field service app solves this by giving technicians everything they need on their phone: job instructions, asset history, service checklists, and more.
For instance, if a technician is sent to repair a machine in a low-signal area, they can still access and complete their tasks using Makula’s offline procedure feature. Once they reconnect, the data syncs automatically, keeping your records up to date without extra effort.
5. Monitor Technician Performance
Keeping track of how technicians perform on the job helps you spot what’s working and what needs improvement. With the right tools, you can monitor work order progress in real time, from dispatch to completion, and review key metrics like job duration, response time, and task accuracy.
For example, if one technician consistently takes longer to complete similar tasks, the data can help you determine whether they need extra support or training.
With Makula, you can set up time tracking tags to categorise tasks and monitor how engineers spend their time in the field. This makes it easier to optimise workloads and identify challenges.
6. Maintain Accurate Machine History
Keeping a complete service history for each asset helps reduce repeat issues and improves accountability. When technicians finalise and sign off on procedures, those records should be automatically centralised and easy to access, both for your team and the client.
This means, if a machine breaks down again months later, engineers can quickly review its service history to understand past issues, parts used, or steps taken. This saves time and prevents guesswork.
With Makula, completed procedures are automatically added to the machine’s service history and made visible to your client. That way, both sides have a clear record of what was done and when.
7. Automate Repetitive Field Tasks
Automating routine tasks helps reduce errors, speed up assignments, and free up your team to focus on high-priority issues.
For instance, instead of sorting through spreadsheets to assign technicians and equipment for repeat maintenance, you can set up predefined workflows. When a recurring service is due, the system automatically creates the work order, assigns the right technician, and reserves any required tools.
With Makula, you can drag unassigned tasks into the calendar, refine the schedule, and assign limited resources like vehicles or specialised tools, all in one streamlined workflow.
8. Use AI to Troubleshoot Faster in the Field
When technicians face unfamiliar equipment or rare issues, every minute counts. AI tools can help them find answers faster by pulling relevant data from past service records, manuals, and internal documents, all in one search.
For example, if a technician is servicing a new model on-site, they can ask an AI assistant for troubleshooting steps and get instant, step-by-step guidance. This reduces guesswork, speeds up repairs, and improves first-time fix rates.
Managing Factory Service Teams? Here’s How Makula Helps
Here’s how Makula can help OEMs simplify and scale their service operations:
Smart Scheduling
Smart Scheduling in Makula helps you stay ahead by letting you plan, adjust, and publish technician assignments with clarity and control.
You can drag and drop unassigned work orders into a calendar, assign technicians based on skill, and attach the tools or vehicles they’ll need. Schedules stay in draft mode until you're ready to notify the team, which helps avoid confusion from premature changes.
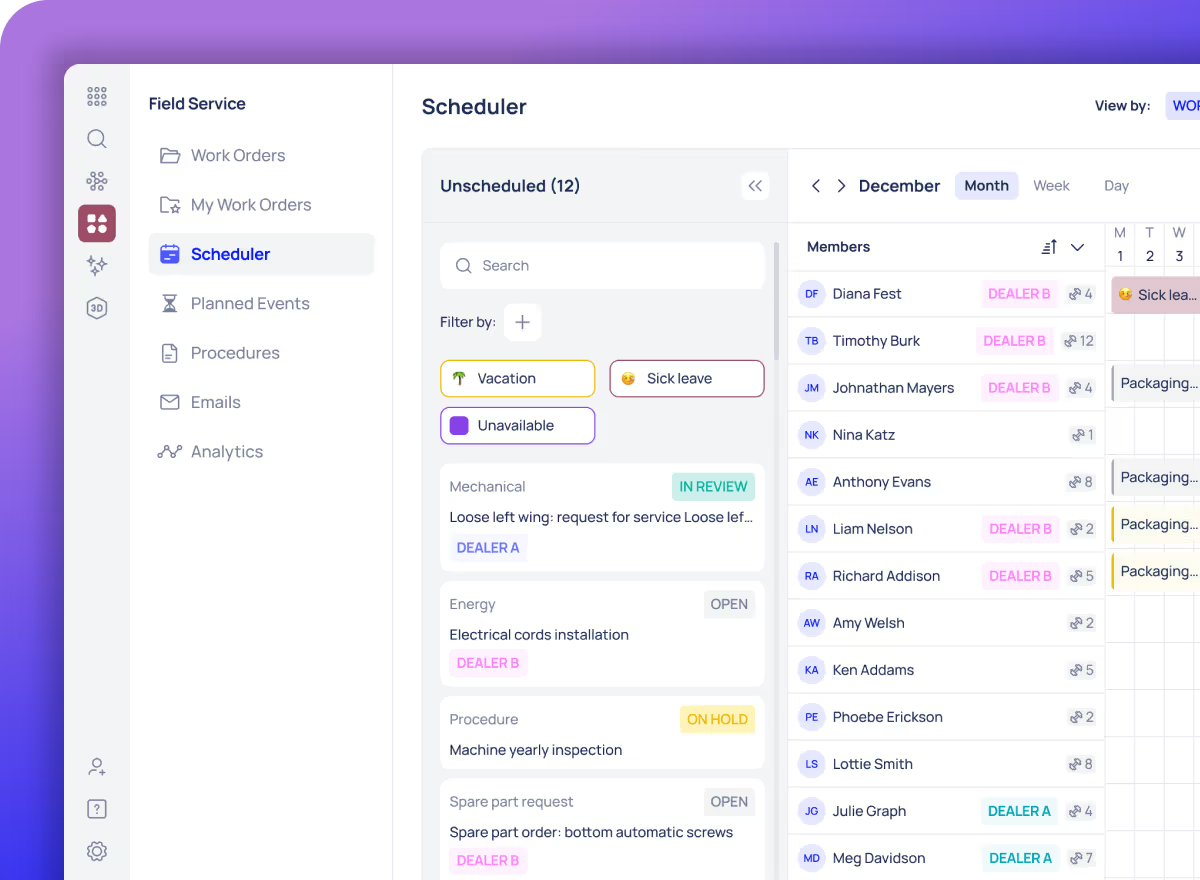
In case two technicians are needed to inspect a failed line at different facilities, you can assign both, reserve the equipment, and publish their schedules once you're confident the timing works.
With Makula, you get daily, weekly, and monthly calendar views, so whether you’re reacting to a machine breakdown or planning out the next 30 days, your service schedule stays organised, visible, and flexible.
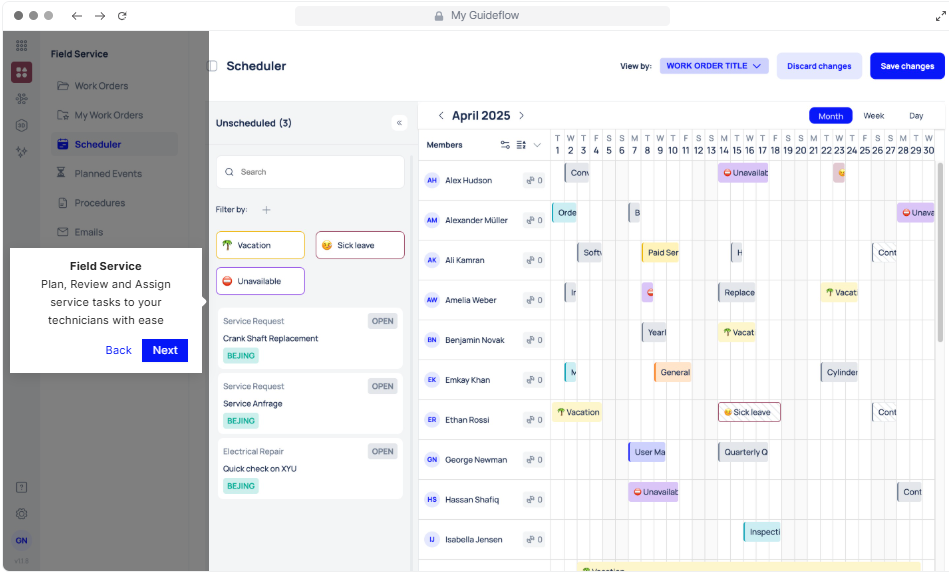
Tracking Procedures for Every Asset
Makula allows technicians to fill out, sign, and finalise procedures directly within each work order, so that every job is properly documented and stored for future reference.
Once a procedure is complete, it’s locked, signed, and marked as final. A PDF version is automatically saved and added to the machine’s history, giving your team and your customer a clear, traceable record of the service performed.
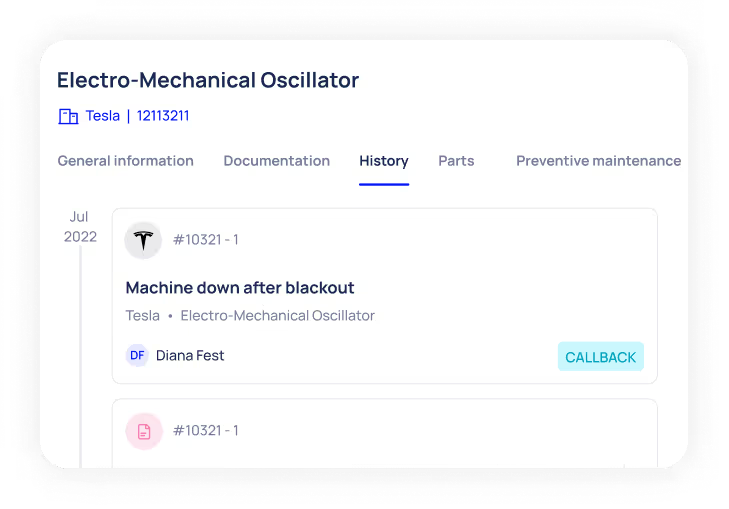
For example, if a motor failure occurs on a production line, the technician can complete the procedure on-site, sign off digitally, and finalise it. That record is then available instantly to both your service team and the factory, helping with compliance, audits, and future troubleshooting.
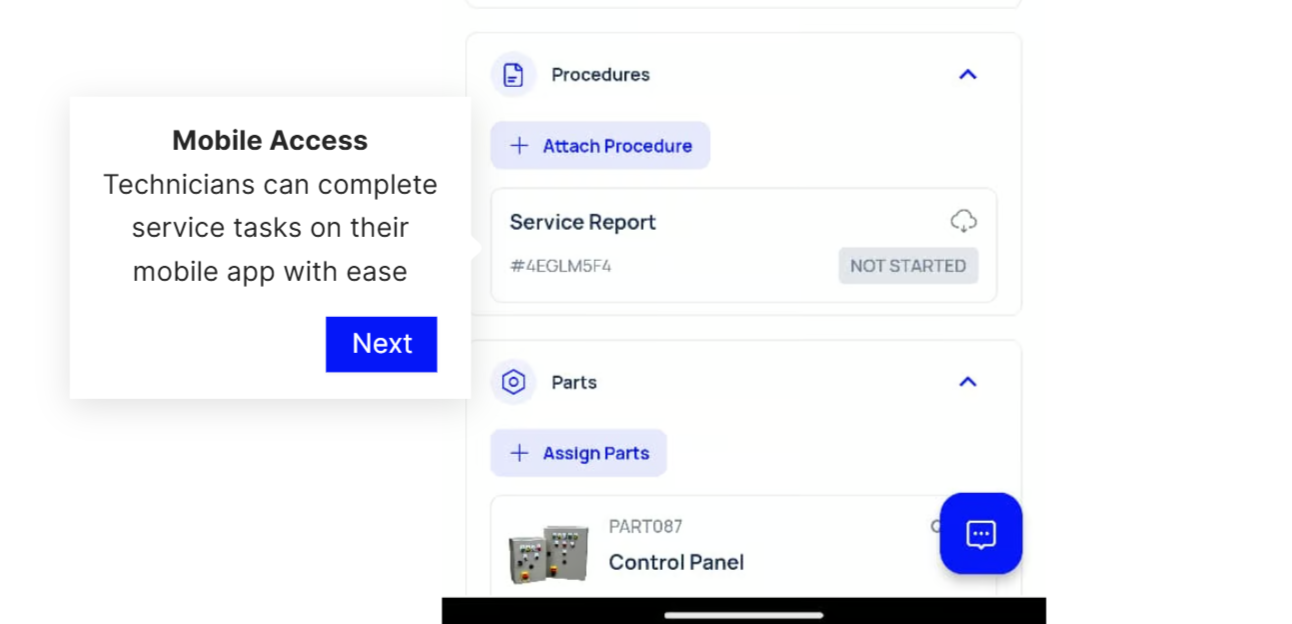
This feature helps you maintain a reliable service trail and build trust through transparent reporting.
Mobile App for Technicians
Makula’s mobile app gives your technicians everything they need, right in their pocket. Technicians can view all work order details, including task descriptions, assigned team members, and attached procedures.
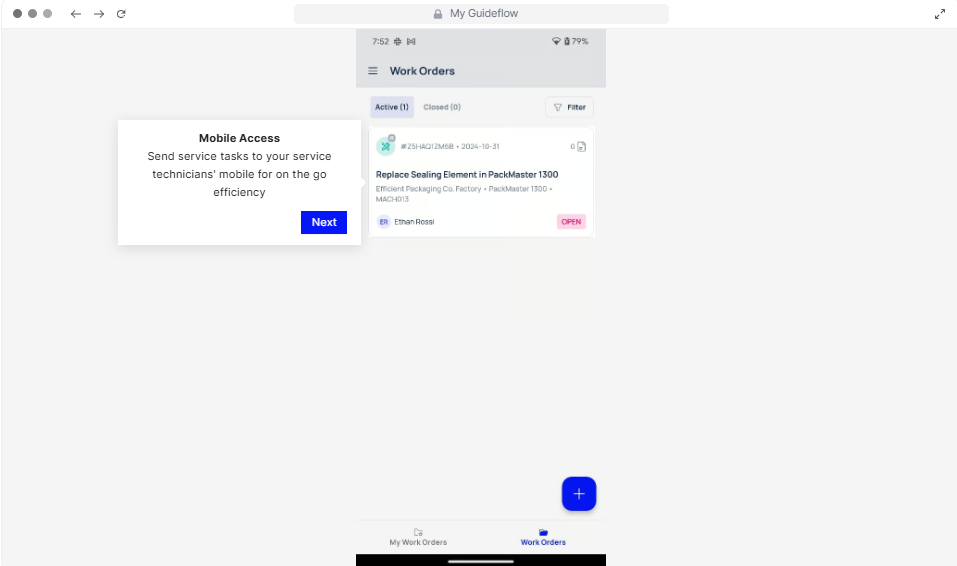
They can fill out digital forms, leave internal notes, and complete job steps directly from the app, without needing a laptop or paper files.
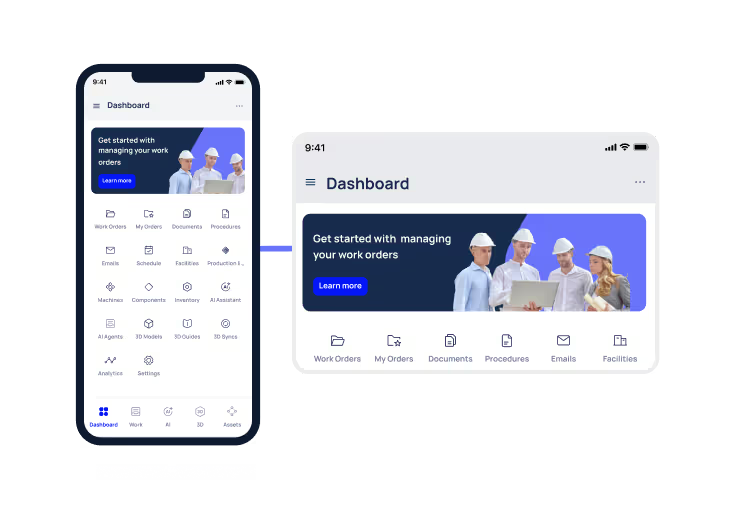
If your technician is dispatched to a remote facility with limited network access, Makula’s offline mode still keeps them connected. They can access saved procedures on their phone, complete the job, and upload the results once they’re back online.
Visual Work Order Management
Makula’s multiple work order views help OEMs stay in control, no matter how complex the workload.
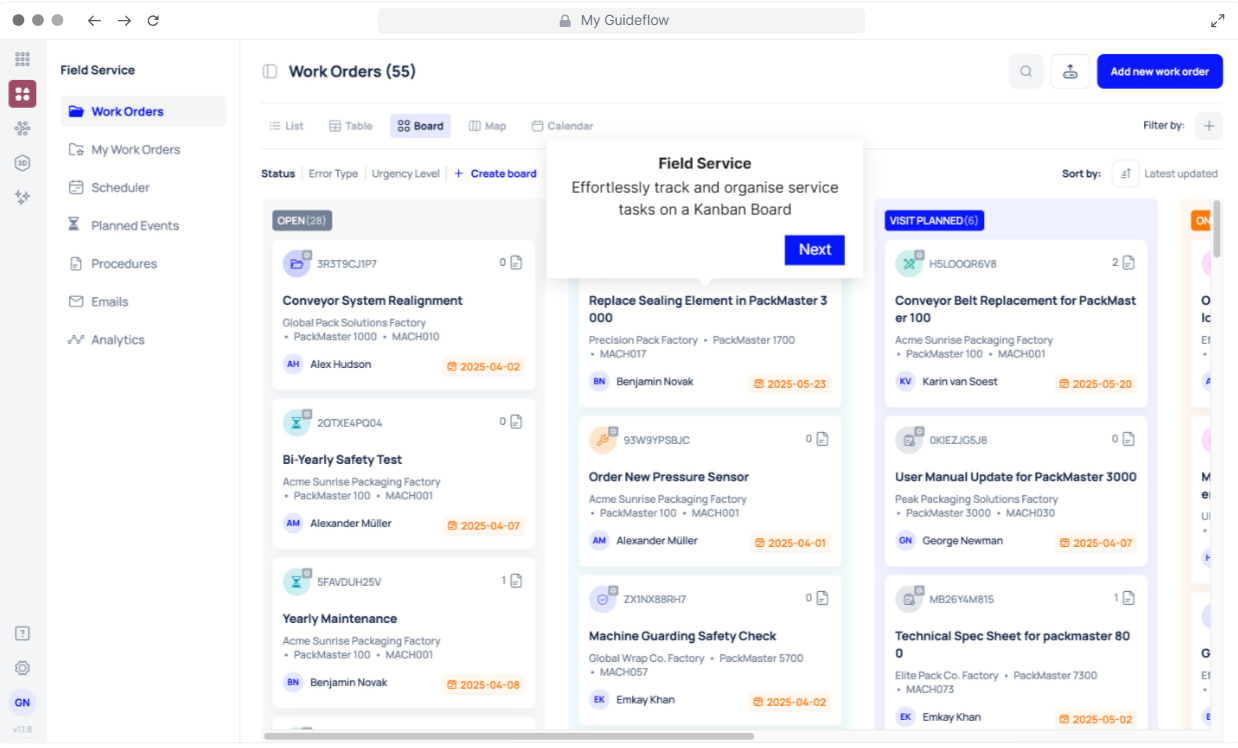
You can switch between five views, each built for a specific use case:
- List View: Get a quick, scrollable summary of all open work orders with key details like assignee, status, and asset information.
- Table View: Review high-volume data with sortable columns like scheduled date, connection contact, and custom fields.
- Board View: Visually track job status using drag-and-drop cards. organise by priority, team, or custom fields to manage workflows in real time.
- Calendar View: See work orders by scheduled date and manage deadlines at a glance. Ideal for weekly or monthly service planning.
- Map View: Plot work orders by factory site to understand geographical distribution and coordinate location-based dispatching.
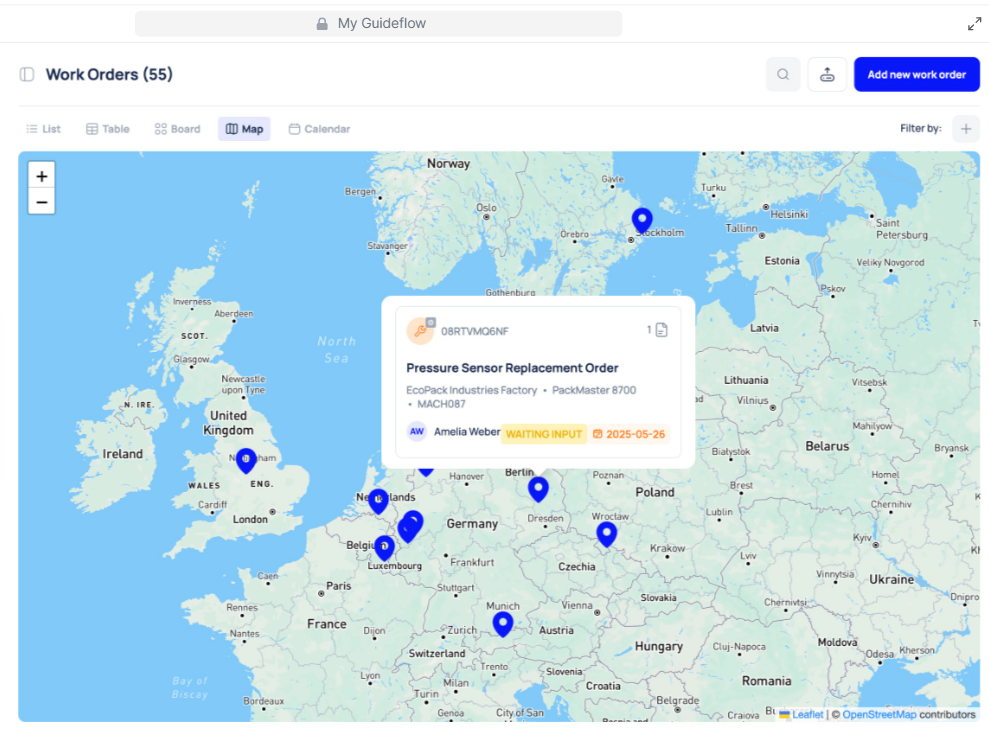
For example, if you need to reprioritise breakdown jobs across multiple sites, you can filter the board by status or priority and reassign tasks instantly.
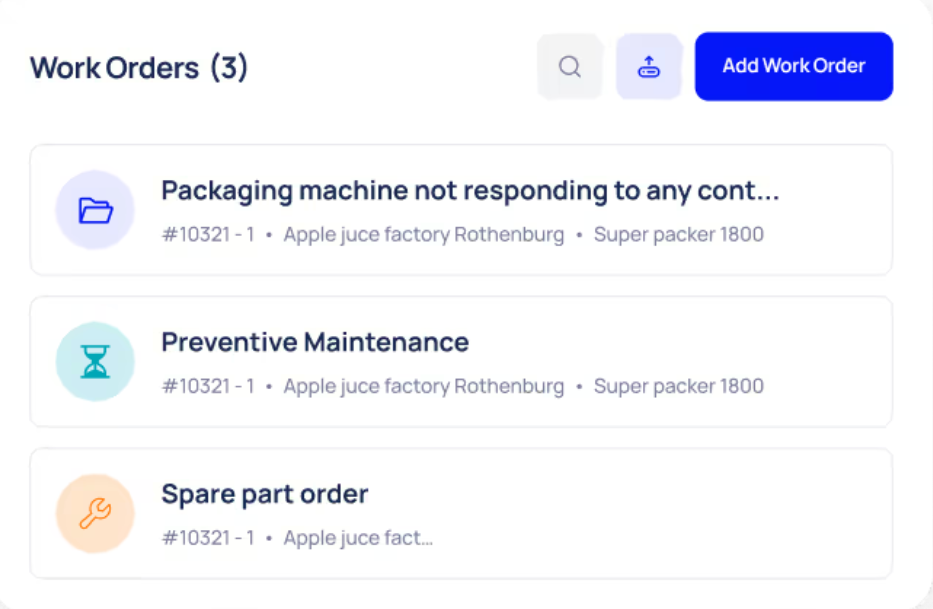
This multi-view setup gives your team the flexibility to plan, track, and adjust, all without switching tools or losing context.
Interactive Analytics Dashboards
Makula’s interactive dashboards bring your service metrics into one place, so you can monitor trends, compare sites, and make informed decisions faster.
You can choose from five chart types: vertical bar, horizontal bar, pie, number, and table, to visualise machine usage or facility-level data. Each chart is customisable, with filters and segments that let you narrow down to the details that matter most.
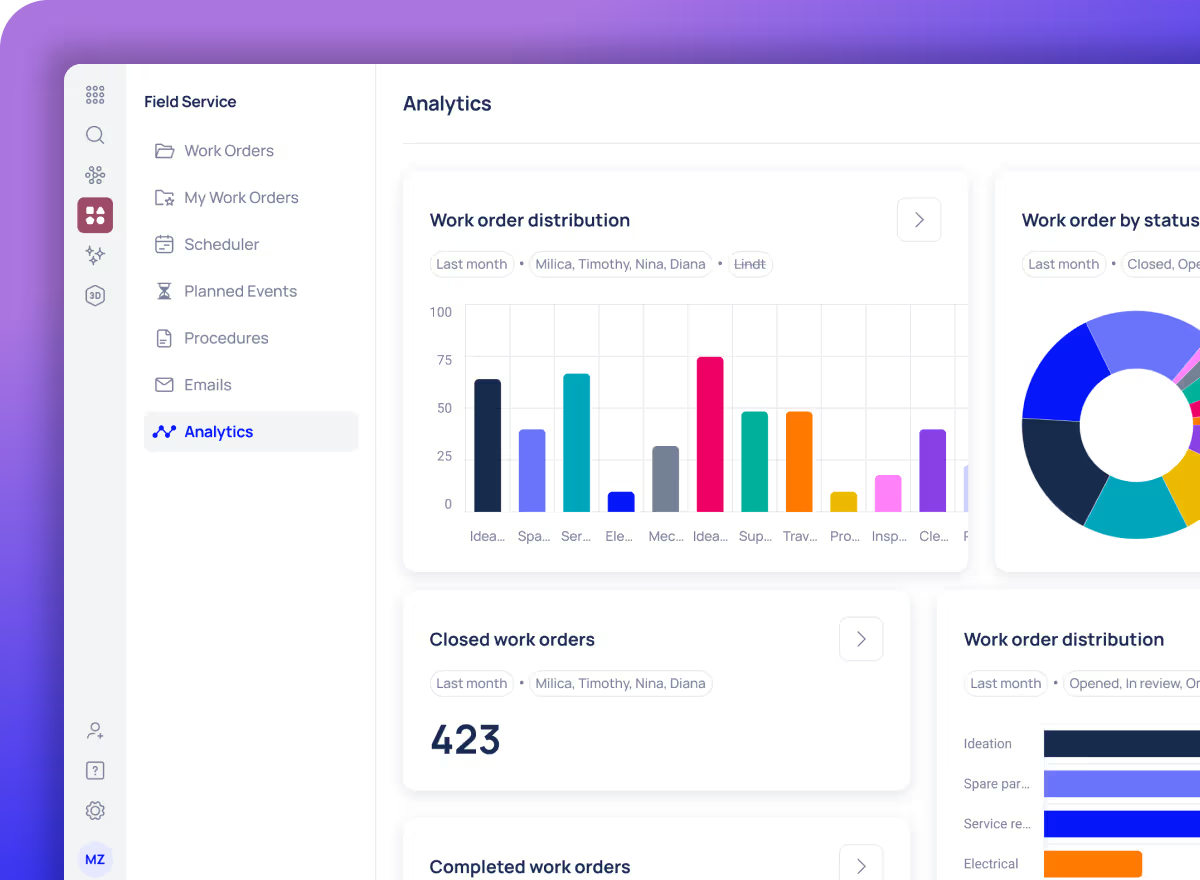
For example, if you're trying to identify which facility has the highest number of open service tickets, you can use a segmented bar chart to break it down by site or priority. Or, if you want a snapshot of total assets under service, a number chart gives you a clean, instant count.
Makula makes it easy to switch views, adjust filters, and track performance without building complex reports, which gives OEMs the clarity they need to manage field service at scale.
Industrial AI Features
Makula’s Industrial AI features give OEM field teams the tools to document, search, and solve issues without wasting time flipping through manuals or typing up notes.
- AI Note-Taking: This feature lets technicians record voice notes during inspections or repairs. The system automatically transcribes and summarises them, so nothing gets missed.
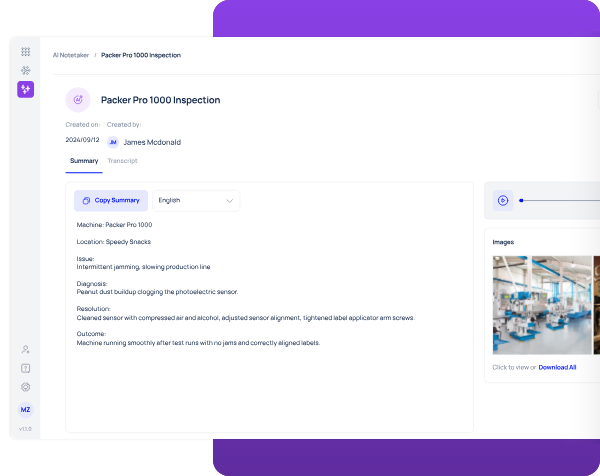
- Enterprise Search: The built-in OCR allows you to unlock old scanned documents, technical drawings, and PDF manuals. Engineers can instantly find the info they need, even from legacy files stored in their archives.
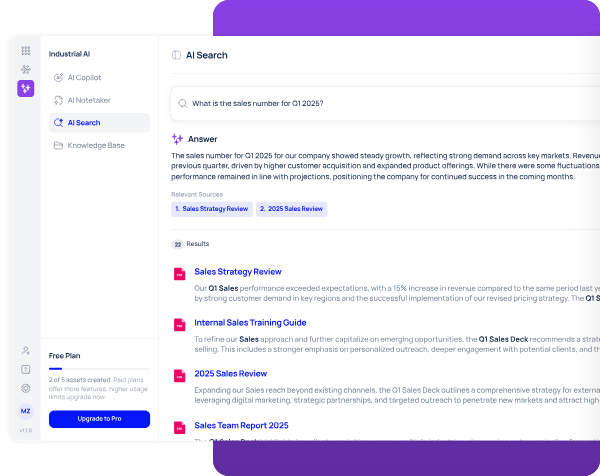
- Machinery Assistant: Available on both web and mobile, this gives technicians direct access to machine-specific data, service records, and procedures, whether they’re in the field, at a desk, or on the plant floor.
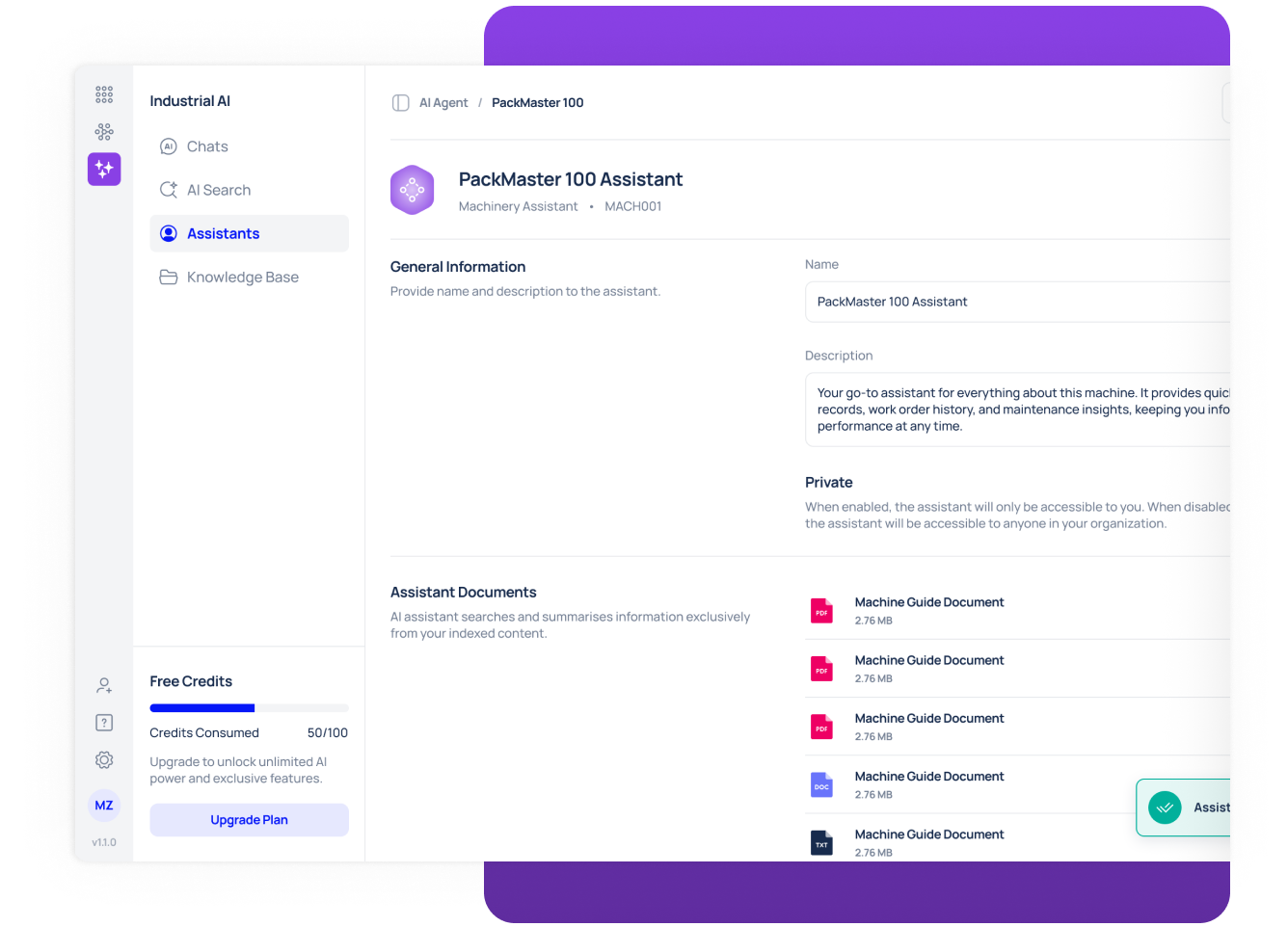
Ready to streamline your field operations and support your technicians where it matters most? Book a demo with Makula and see how it helps OEMs plan smarter, respond faster, and deliver consistent service